Today’s post covers overmolding design success tips for designing company prototypes. Can you quickly tell the quality of a pair of pliers by just looking at it? Will the battery pack of a drill drain fast after you pull the trigger? Can you determine a product’s overall integrity based on its appearance or how it feels in your hands? Believe it or not, you’re not the only one who doubts some products before you touch or use them. Even the most minor design details can provide insight into the material’s sturdiness and the quality of the engineering design services and applications used.
Before a product comes to fruition, companies create several prototype designs, where overmolding enters the picture. Overmolding is a feature that can take the appearance and feel of a product to the next level. It enhances aesthetics, performance, and functionality, making it more popular and in demand among manufacturing prototype design firms for portable devices, medical devices, and consumer products. Continue reading to know more about the strategic considerations to ensure a successful overmolding design:
RELATED: Different kinds of prototypes and how to use them for your design project
What is overmolding?
Overmolding refers to the process of making one part using the combination of two or several different materials. The first material, the substrate, is often fully or partially covered by overmold or subsequent materials throughout the manufacturing process. The substrate can be anything, including a molded plastic part, a machined metal part, or even existing products such as electrical connectors, screws, or threaded inserts. This first piece will soon transform into one continuous part of often mechanically interlocked and chemically bonded materials of different types.
Overmold materials, usually plastic, begin in pellet form. The design for additive manufacturing company combines the pellets with additives such as foaming agents, colorants, and other fillers. These are heated afterward to their melting point before they’re injected in liquid form into the mold tooling. There are several limitations on the types of materials suitable for use for overmolding. If you’re overmolding a metal part with plastic, any plastic can be used. There might be compatibility issues if you’re overmolding a plastic part with a different type of plastic, TPE, or rubber.
The material manufacturer often releases compatibility charts for overmolding. As a unique process of custom injection molding and casting services, overmolding leads to the seamless mixture of several materials into one product or part. It often involves a plastic-base and rigid component overload with rubber-like, pliable, and thin TPE or thermoplastic elastomer exterior layer or other types of materials with the use of either two-shot or multiple-shot molding method or a single-shot or insert molding. After considering its benefits, plastic overmolding may be ideal for your company’s projects.
Common uses and applications of overloading
Overmolding is used for different reasons that may vary based on the specifics of a particular project. Some of the common materials where the process is used include personal care items and tool handgrips. Below are several typical applications of overmolding:
Plastic over plastic
Molding a rigid plastic substrate is the first step. Another rigid plastic will be molded around or onto the substrate. These plastics may differ in resin or color.
Rubber over plastic
A rigid plastic substrate is molded first. TPE or soft rubber is molded around or onto the substrate. It typically creates a soft grip spot on a tricky area.
RELATED: How to design products for injection molding & prototyping firms
Plastic over metal
A metal substrate is formed, cast, or machined. The substrate will be inserted into the injection molding tool. The plastic is molded around or onto the metal. It is usually used for capturing metal components in the plastic part.
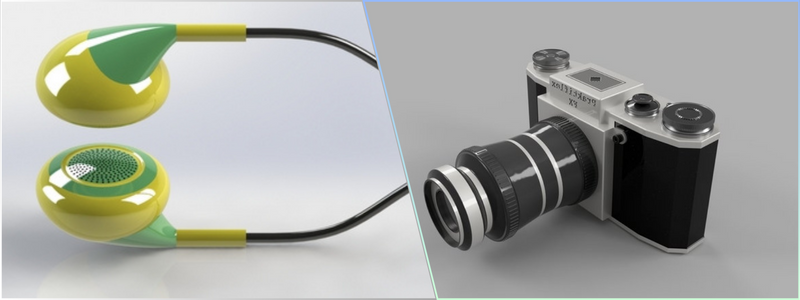
Rubber over metal
A metal substrate is cast, formed, or machined. The substrate will be inserted into the injection molding tool. The TPE or rubber will be molded around or onto the metal. It is usually used to create a soft grip surface. However, there are compatibility issues and limitations when using different materials. It also doesn’t mean that you can only use two materials. It’s common for 3D product modeling companies to design products where one part uses three materials to achieve grip surfaces and color breaks.
The overmolding process
The substrate part or material is typically placed into the injection molding tool. The overmold material is then shot around, onto, or into the substrate. Once the overmold material solidifies or cures, the two materials will be combined to form a single part. It is often a good idea for the mold material and substrate to interlock in a particular mechanical capacity. It will help ensure the two materials are physically held together and not just chemically bonded.
RELATED: Which manufacturing technology is right for your new invention?
Strategic considerations before overmolding design
Although the overmolding process is cost-effective and can offer outstanding adhesion between the materials, proper planning is required to ensure its success. The machinist, for example, should choose suitable materials to achieve optimum adhesion and carry out the function of the part. It is one of the main reasons why the machinist should have proper planning of the overmolding design guide.
Since the design is often complex, you must be extra careful when developing the overmold design.
Consider the following elements that contribute to the success of the design, ensuring its effective realization.
The function of the part
A complete understanding of the part’s intended function plays a significant role in successfully designing an overmolding part. For this to be possible, you must ask several questions about the part.
RELATED: An overview of injection mold materials and SPI standards for companies and firms
1. What is the proposed objective or purpose of the part?
The design process must first understand the purpose of designing the part. Since overmolding has several uses and applications, knowing the goal of the product is essential to determine the suitable process to use. If you’re planning to have a seal molded on a water-resistant case, the goal of the product is a waterproof seal.
2. What kind of exposure will the part endure and deal with?
You also need to consider the kind and amount of exposure the product will be dealing with when it’s in the line of duty before you develop a design. If the part endures harsh radiation such as UV light, this type of product can use certain plastics.
RELATED: Injection molding tips for cost-effective prototypes and mass-manufacturing by a mold design firm
3. Why do you want to mold the part over?
The main reason why you plan to use overmolding for the part can help you determine the complexity of the design. If you hire an injection mold designer to develop a TPE overmolding design guide for rubber-like or TPE to be cast on a product handle, the proposed gadget could be for grip, comfort, ergonomics, or vibration absorption. A satisfactory answer to this question will help you determine the most appropriate material and map out a correct overmolding design guide.
4. Will the part receive a large-scale production?
If the part is planned for large-scale production, you must consider it when developing your overmolding design guide. For example, an overmolding part intended for vibration dampening will feature a thick wall that will require a longer cycle time and more materials to produce each part. Making this kind of product can get quite costly, although it might be worth the investment if you only need several pieces.
RELATED: Prototype injection molding: 7 materials commonly used by design firms
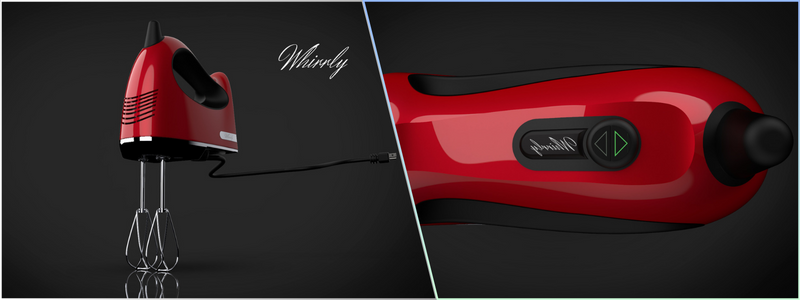
Scenario
Once you have confirmed that the function of the part will fit in with the design, your next step for the 3D design services is to evaluate the instances where it will be used and their effect on the physical features. The following are the four most common scenarios where overmolding products are used:
1. Grip addition to a substrate
Different products, including kitchen utensils, garden hoses, and drills, require a certain amount and level of grip that allows users to control the product even under wet conditions. In cases like this, the most recommended way to add grip to such products is to cast rubber-like plastic over the handles. This process only needs a little material and may only need production in low quantities more often than not.
2. Comfort
When the grip is added to a substrate, this also acts as a source of comfort every time the product is used. The scenario is the same as the first point in most cases. The rubber grips used on bicycle handles are the perfect example of products that combine the two scenarios.
3. Sealing
This scenario requires longer cycle times and more materials to make an overwhelming product. These seals often feature water-resistant properties and must achieve optimum substrate adhesion. Before you design this type of part, looking for the material that will create the maximum adhesion with the substrate and offer the highest form of waterproof abilities is essential.
4. Vibration dampening
This specific type of usage not only has the longest cycle time but also needs the most amounts of materials. The TPE part that will be produced must have an adequate thickness for absorbing the vibrations of the substrate you plan to cast it on. This scenario is applied to most high-energy machines, such as drills and pumps.
How Cad Crowd can help with overmolding design
Contact Cad Crowd to help you find the best overmolding experts to help you with the following prototype designs for your company. Get a free quote now.