This article covers injection mold materials and SPI standards for firms and companies. Molded parts can be seen almost anywhere, from the notably cosmetic housings that hide in plain sight to the internal components that don’t require fine polish. For an average person, the surface finish of these parts is almost negligible. However, things are different for product designers, injection mold designers, and engineers because the surface finish is a critical consideration in the design process.
What is injection molding?
Production of parts in large volumes is possible with the help of injection molding services. This process injects molten materials into a mold, often used as a mass production process for manufacturing identical items in huge numbers. Injection molding materials include glasses, metals, confections, and elastomers, even though it is most frequently used with thermosetting and thermoplastic polymers.
RELATED: How to design products for injection molding & prototyping firms
Injection molding has numerous applications in manufacturing, specifically for producing high-volume and custom parts. Although the molding and tooling are often pricier, the production cost is low once completed. With the ability to create almost identical components, injection molding is used for parts in various materials.
What is SPI?
SPI, or the Society of the Plastics Industry, sets the standards for the plastics industry in the US. SPI is a trade association based in the United States that is now called the Plastics Industry Association or simply PLASTICS or PIA. It is one of the standards regulating the polish used on molded plastic products.
The SPI guidelines offer product designers and injection mold design experts a standard way of describing the surface finish of the molded plastic parts. By providing a common language for the different surface finishes, the SPI standards make it easier for companies and firms to request and receive injection molded parts with specific textures or polishes.
What are SPI surface finishes?
The SPI sets the SPI surface finishes as the surface finish standards generally accepted globally and referenced by injection mold designers. The standards cover the 12 different grades of SPI mold finishes. Note that the terms SPI mold finishes and SPI surface finishes are used interchangeably in this sense. The SPI guidelines define the 12 standards for the injection mold finish, and each one has an alphanumeric identifier that starts with letters A, B, C, and D and ends with the numbers 1, 2, 3, and 4. You will also sometimes see a dash between the numbers and letters.
There is a surface roughness average or RA and a finishing method for every alphanumeric SPI standard. Finishing methods use particular types of dry blasting, diamond abrasive, stone abrasive, or grit paper. RA is measured in terms of micrometers represented by the symbol µm and given as a range of different values. It is also important to remember that SPI standards are categorized into four grades: A for glossy, B for semi-glossy, C for matte, and D for textured.
There are also three SPI callouts under each of the four different grades, with the 12 SPI callouts having unique attributes. A diamond abrasive is applied to attain a glossy finish, stone abrasive is used for a matte finish, dry blasting is for a textured finish, and grit polish paper is for a semi-glossy finish. The mold level chart below describes the 12 different SPI surface finishes, including their specific typical surface roughness and finishing method.
RELATED: Which manufacturing technology is right for your new invention?
SPI Standard | Finish (Grade) | Finish (Type) | Finishing Method | Typical Surface Roughness |
A-1 | Glossy | Super | Grade #3, 6000-Grit Diamond | 0.012 to 0.025 |
A-2 | Glossy | High | Grade #6, 3000-Grit Diamond | 0.025 to 0.05 |
A-3 | Glossy | Normal | Grade #15, 1200-Grit Diamond | 0.05 to 0.10 |
B-1 | Semi-Glossy | Fine | 600-Grit Paper | 0.05 to 0.10 |
B-2 | Semi-Glossy | Medium | 400-Grit Paper | 0.10 to 0.15 |
B-3 | Semi-Glossy | Normal | 320-Grit Paper | 0.28 to 0.32 |
C-1 | Matte | Fine | 600-Grit Stone | 0.35 to 0.40 |
C-2 | Matte | Medium | 400-Grit Stone | 0.45 to 0.55 |
C-3 | Matte | Normal | 320-Grit Stone | 0.63 to 0.70 |
D-1 | Textured | Satin | Dry Blast Glass Bead #11 | 0.80 to 1.00 |
D-2 | Textured | Dull | Dry Blast #240 Aluminum Oxide | 1.00 to 2.80 |
D-3 | Textured | Rough | Dry Blast #24 Aluminum Oxide | 3.20 to 18.0 |
The SPI standard also specifies an as-machined finish with visible machining marks and 3.20 RA typical surface roughness for injection mold that don’t require any of the above surface finishes.
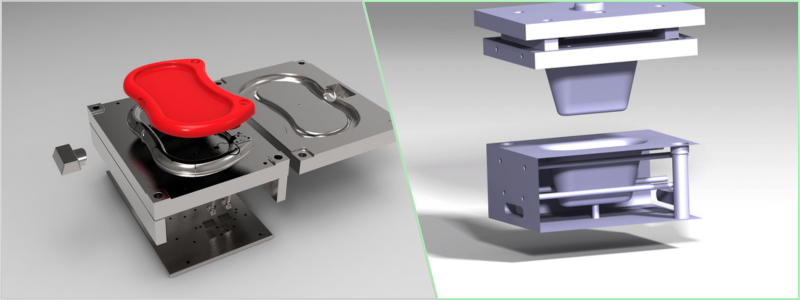
Injection mold materials and SPI standards
Now that you know the SPI guidelines and the basics involved in surface finishing, the next step is to consider the different injection mold materials available for you to choose from. Injection mold designers need to know and understand that every SPI mold finish produces different results according to your selected injection molded plastic. The specific material the parts have been developed from will determine the results you can expect from a textured or polished mold.
RELATED: Prototype injection molding: 7 materials commonly used by design firms
In addition to surface finishes, you may also consider utilizing injection molding and casting services. These services provide expertise in manufacturing plastic parts through injection molding and casting processes for other materials. Injection mold design experts can assist in designing, producing, and finishing various components according to your specific requirements.
Here are the outcomes you can anticipate when specifying a glossy, matte, semi-glossy, or textured SPI finish for the injection molded plastic parts to your injection mold design expert. You will also find tables for several common injection molding materials and examples of their application.
1. Glossy finishes
The SPI glossy finishes, as their name suggests, are extremely shiny. Injection mold designers often use these finishes for high-polish parts such as mirrors, clear cases, and optical lenses.
- SPI A-1 is for highly polished, optically clear, or transparent parts.
- SPI A-2 is for highly transparent or polished parts.
- SPI A-3 is for parts needing medium to high polish or non-optical lenses.
The table below reveals that injection molded acrylic always offers an exceptional surface finish:
Plastic | A-1 | A-2 | A-3 |
ABS | Average | Average | Good |
Acrylic | Excellent | Excellent | Excellent |
Nylon | Average | Average | Good |
Polycarbonate (PC) | Average | Good | Excellent |
Polypropylene (PP) | Not recommended | Average | Average |
Polystyrene (PS) | Average | Average | Good |
2. Matte finishes
Instead of shiny, SPI matte finishes are dull and used in specific applications like injection molded laptop frames and keyboards. Since SPI C-3, SPI C-2, and SPI C-1 finishes tend to reflect less light, the fingerprints are less noticeable on frequently handled products compared to a highly polished finish. These matte finishes also apply to product designs that injection mold designers require a more muted or subdued appearance.
RELATED: How to save money on injection molding: 10 tips from an engineering design firm
Plastic | C-1 | C-2 | C-3 |
ABS | Good | Good | Excellent |
Acrylic | Good | Good | Good |
Nylon | Good | Excellent | Excellent |
Polycarbonate (PC) | Good | Good | Average |
Polypropylene (PP) | Good | Good | Excellent |
Polystyrene (PS) | Excellent | Excellent | Excellent |
3. Semi-glossy finishes
The SPI semi-glossy finishes shine differently from their higher gloss counterparts. This is why SPI B-3, SPI B-2, and SPI B-1 are ideal options for injection mold designers for parts like injection molded clips that require a medium shine. Given the table below, you will notice that you can expect an excellent finish from polystyrene parts and good results from many of the listed plastics.
Plastic | B-1 | B-2 | B-3 |
ABS | Good | Good | Excellent |
Acrylic | Good | Good | Good |
Nylon | Good | Excellent | Excellent |
Polycarbonate (PC) | Good | Good | Average |
Polypropylene (PP) | Good | Good | Excellent |
Polystyrene (PS) | Excellent | Excellent | Excellent |
4. Textured finishes
The SPI textured finishes apply to products like steering wheels and shop vacs that injection mold designers fabricated to be held and gripped in hand. Even though SPI-D3, SPI D-2, and SPI D-1 surface finishes offer outstanding results with several typically used plastics, the designers should avoid choosing polycarbonate as the material for injection molding if the mold finish is SPI D-3 or SPI D-2.
Plastic | D-1 | D-2 | D-3 |
ABS | Excellent | Excellent | Excellent |
Acrylic | Average | Average | Average |
Nylon | Excellent | Excellent | Good |
Polycarbonate (PC) | Excellent | Not Recommended | Not Recommended |
Polypropylene (PP) | Excellent | Excellent | Excellent |
Polystyrene (PS) | Excellent | Excellent | Good |
How to choose the best SPI surface finish for injection mold parts
The truth is that the surface finishes on injection mold parts are not identical to those of CNC-machined or 3D-printed parts. With CNC machining services and 3D printed parts, surface finishing happens after manufacturing the part. With injection molded parts, the mold surface is textured or prepared for the part to come out of the already finished mold. This implies that when a matte finish is desired for the intended part’s design, the mold’s interior will be appropriately textured to ensure the part achieves the desired matte finish upon removal from the mold.
RELATED: Top 9 design engineering tips for reducing manufacturing costs on new product designs & prototypes
Through this, part injection mold designers can better understand the SPI surface finish that is most suitable for the injection molded part. If the injection mold designer needs more visually appealing parts, they can also texture the mold inside to suit their aesthetic requirements. For instance, a resulting smooth or matte texture on the part’s surface will give a more desirable aesthetic and hide minor imperfections like sink marks, shadow marks, flow lines, and knit lines caused by the mold. Many consumers find it more desirable and appealing if a product has a more eye-catching surface finish.
How Cad Crowd can assist
Given the many design considerations for injection molding, it takes special skills, training, and knowledge to implement all of them and get the part right. This is something only experts are capable of, and you will find plenty of them through Cad Crowd. With our broad network of experienced engineers and product designers, we can provide you with an individual or a team of professionals who can help you develop injection molded parts from scratch. We will match you with pre-vetted and highly qualified design professionals. Get a free quote today, and tell us about your project!