Maximizing quality while minimizing cost is the main goal of any product commercialization specialist. Such a feat is the crux of any competitive product-providing business and is pivotal to a company’s vertical expansion.
Production costs are often contingent on many factors and finding the right ones to cut without damaging your product along with your business’s reputation is no small feat.
Here, we’ll cover a few great tips to reduce your manufacturing costs on new designs and prototypes without hurting your market offering. But first, we’ll shed some light on the CAD design process itself so you know what to expect.
The Design and Engineering Process In a Nutshell
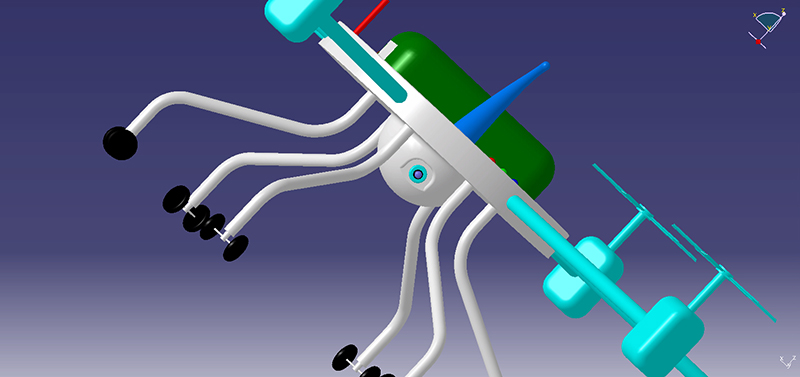
Designing and engineering, as they pertain to product development, can be thought of as two separate processes of equal importance. Both can be handled by the same team or person and are essentially intertwined.
Designing a Product
Product design can be considered a far more artistic aspect of product development than engineering. The design process concerns itself with the aesthetic qualities desired, functionality required, and regulations to be met. In short, it can be described as follows:
Identifying a Problem
This pivotal first step in product design is largely handled by the company as opposed to the hired designer. Market research and surveying can likely provide you with all of the information you may need to handle this step on your own.
Solving the Problem
It is here that designers typically come into the picture. From your key ideas, designers visually develop a product capable of solving the problem you’ve identified.
Refining the Solution
This is the iterative phase of every product’s ongoing development. In effect, this stage of the product’s design may never truly come to a close. Over time, tweaks and improvements are almost entirely inevitable and the product you begin producing may not look anything like its refined counterpart from the future.
Product Engineering
This part of the product development process deals with the creation of a production system for the item in question. Product engineers may not necessarily concern themselves with details such as an item’s utility or appearance, but instead concentrate the bulk of their efforts on creating a safe, reliable specification for crafting your product.
Why Manufacturing Costs Matter

Manufacturing costs matter for the very same reasons all other operational costs of a particular business matter; they affect a company’s bottom line.
Market Costs Can Pile Up Quickly
Costs can quickly gain momentum if you aren’t keeping up with them and, before you know it, they could pile precariously high, threatening to match or exceed your profits. Here’s a quick rundown on the costs involved with creating products to sell.
- The ‘cost of goods sold‘ is comprised of only the direct costs of production, including materials and labor. These costs are often rather straightforward to quantify.
- Distribution costs are all expenses that arise from logistics. These include the price of delivery from the factory to your warehouse or fulfillment center and subsequent shipping to customers as well as retailers.
Sales team and advertising costs are those incurred for all forms of marketing and the labor involved in managing marketing campaigns, etc.
The Bottom Line
Turning a profit with your new product generally comes down to a simple formula:
- Sales Price – Total Expenses = Profit
Your business’s total expenses are likely to be primarily comprised of your product creation expenses. To improve the profitability of any product, you’ll need to better manage the necessary costs involved in producing it.
Reducing manufacturing costs on new product design and prototype design services can be done in many different ways. Below are a few solid tips for tackling this issue during the design and engineering stages of your product’s development:
Design Tips for Reducing Manufacturing Costs
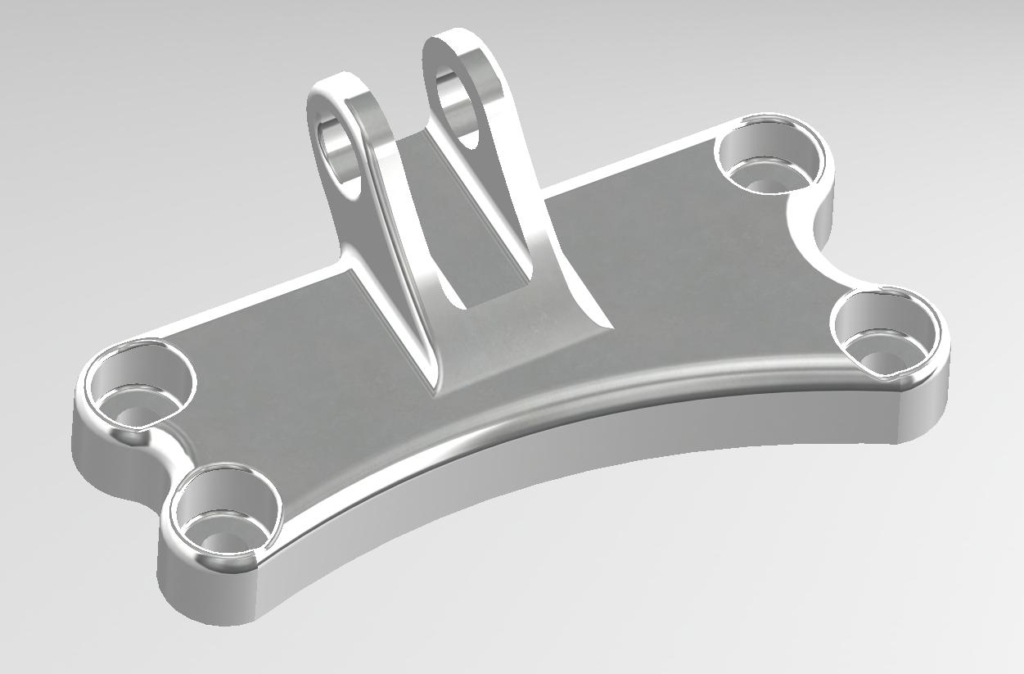
The design process provides plenty of wiggle room for production price considerations. In fact, this process often determines over 50% of your product’s final manufacturing price. In contrast, the cost of a quality product design is negligible, estimated at a mere 5% of total expenses in the production process.
Due to the reasons stated above, maximizing product profitability is best done at this stage of development, before engineering tasks are tackled at all. Here are a few cost-management tips for minimizing the costs of manufacturing services as your product takes shape:
1. Design for Manufacturing
Designing for manufacturing is a specialized approach to designing that prioritizes ease of product creation over other factors. However, despite centering on the ease with which an item can be manufactured, this technique is particularly helpful for minimizing costs across the board. After all, manufacturing costs are mostly contingent on the relative difficulty of crafting your product.
This approach changes depending on the product and manufacturing processes you apply it to, but physical products share similar requirements. To begin effectively designing a physical product for manufacturing, you’ll need to take the key points that follow into consideration:
Minimize Set-Up (Fixturing or Tooling)
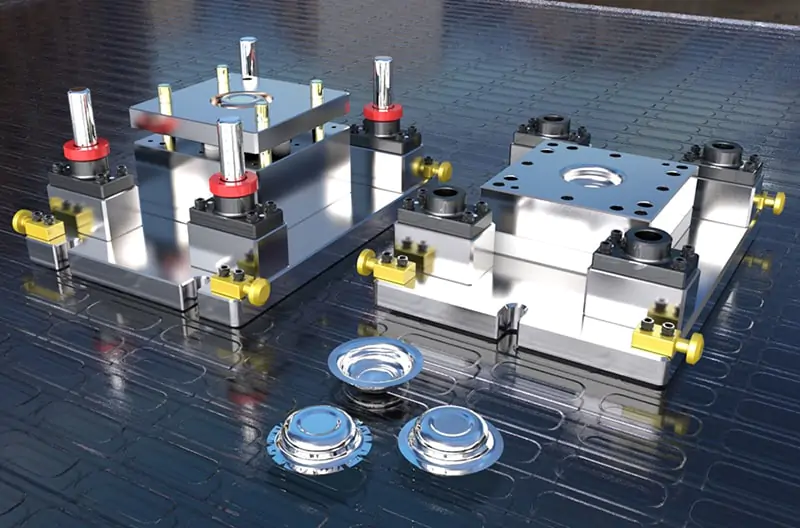
Set-up or fixturing is the process of physically flipping a part during the building process. This applies largely to CNC machining and can be the cause of significant price discrepancies due to relatively small design flaws.
To optimize this part of the production process, you should focus on developing a product design that can be built with minimal flipping and re-orientation during machining.
Use the Ideal Form of Your Chosen Material
The many types of plastics, metals, and other materials you have to choose from present diverse challenges and benefits in the production process, but an often overlooked aspect of choosing materials is the form they come in.
Once an appropriate metal has been chosen, for instance, differentiating between its bar, sheet, and plate forms can help to drastically cut costs, as certain forms are often cheaper than others.
Use Proper Part Tolerances
A manufactured part’s tolerance is the degree to which its exact dimensions can vary without it becoming unusable. Small differences in size creep into most manufactured products, but big differences are usually inexcusable.
Specifying a high degree of precision as necessary for each of your product’s parts may seem ideal, but this is a surefire way to blow up the price. Instead, aim for a functional blend of high precision parts with low tolerance and low precision parts with high tolerance.
- High precision pieces are usually those that require further assembly
or attachment to each other.
- Low precision pieces tend to be outer coverings and standalone parts
that require no precise connections to other parts.
2. Consider the Materials
Material options are vastly varied in modern manufacturing, and each has a host of characteristics worth keeping in mind as your product is designed. There’s much more to materials than available form factors. Here are a few key points to keep in mind:
Consider Material Finishes
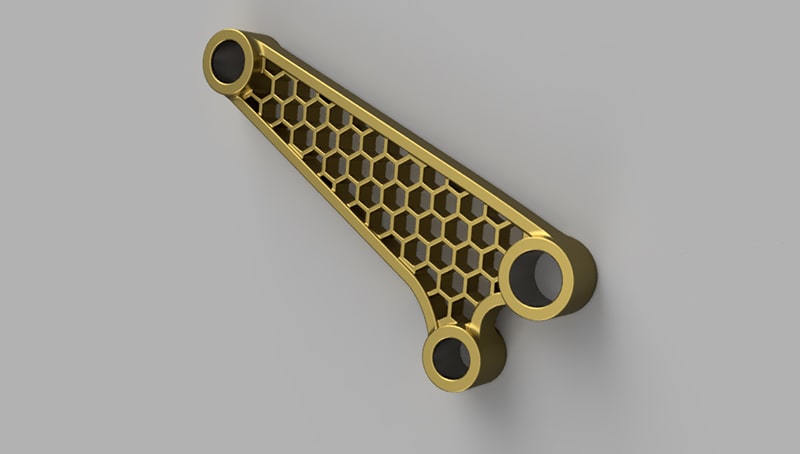
Accounting for different pricing for certain material finishes helps to gauge the overall cost of your product’s manufacturing process.
Injection molds, for example, can be polished to varying degrees, each more expensive than the last. This defines the upfront price for mold tooling but will not apply to individual parts once production begins.
Choosing less refined finishes ensures lower tooling prices and might not negatively affect your finished product’s appearance. The effect is far more pronounced if your product is to be produced through the use of CNC machining as individual parts will require finishing.
Minimize Manufacturing Waste
Waste of any kind in the manufacturing process is costly. Lean manufacturing as a concept centers on the elimination of such wasteful aspects of production as defective products, scrap material,
A simple rule
- Defective products can be caused by failings on the manufacturer’s side of the equation, but design plays a significant role as well. Your best bet to avoid this while still in the design phase is active collaboration with a manufacturing engineer to ensure specific details that increase the likelihood of defective products being created are handled early on.
- Scrap material is any material leftover after a product or group of
products have successfully been built. Tackling this issue during the designstage of your product’s development often comes to setting higher tolerancesfor parts that are neither functionally nor aesthetically critical. Aswas mentioned above, high tolerance and low precision make forcheaper production . They also make for less scrap material being removedto account for especially specific sizing, etc.
Another scrap reduction option is to include as many individual parts per piece of material as is safely possible. In injection molding, this means creating molds capable of producing the maximum number of parts in a single shot.
3. Consider Hollow Structural Options
In injection molded products and parts, the thicker the wall of the part, the higher the chance of problems arising during production. All manner of defects can creep into thick walls in this type of production process, severely affecting production costs by making the overall process more complex.
Clever design techniques minimize these kinds of risks by adopting the use of structural elements such as ribs and gussets, which provide significant strength improvements in thin-walled parts without the difficulties associated with thicker walls.
Apart from minimizing defects in production, using hollow structures for a product wherever possible allows for less material overall to be used to produce each part. Less material makes for lower expenses. If your parts are being injection molded, then less material also equals less cooling time per piece, which compounds the potential for savings.
4. Keep Physical Prototyping to a Minimum
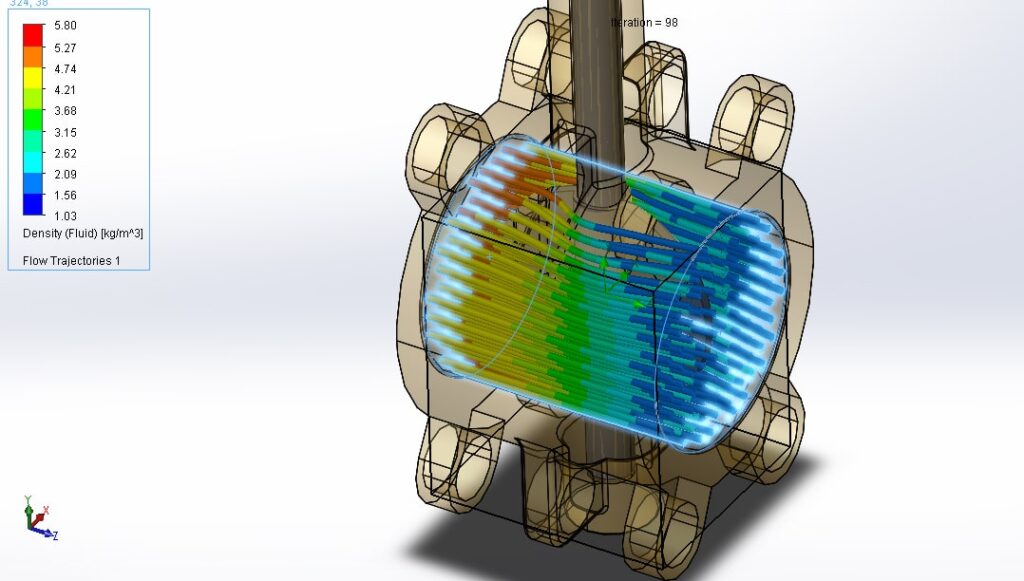
Physical prototypes are an essential part of any product’s development process, but relying on them too heavily can cost you quite a lot of money.
Through the use of iterative CAD development, you can work out a lot of the kinks in your product before you need a physical prototype at all. Software-aided performance tests reinforce this possibility with highly accurate specialized options available to separate industries for stress testing parts and materials.
Engineering Tips for Reducing Manufacturing Costs
The engineering process poses much potential for product cost reduction. Skilled engineers consider numerous factors as they create a suitable production process or system.
Cost-reduction engineering, as its name implies, deals entirely with the optimization of pricing in the manufacturing process. There are many approaches to this task and techniques to take into account. Here are a couple of helpful options:
5. Consider Value Engineering
Value engineering centers on the refinement of a product’s implicit functions in relation to its overall manufacturing cost. Functional yet cost-effective products are always the end goal in this process.
However, engineering services take into account each of a product’s functions throughout the process of its design and discards those that add insufficient consumer value. It’s a scientific process of sorts that asks what something does and whether that something is needed at all.
An example of the above would be the omission of a rubberized grip on a writing pen to keep costs and complexity to a minimum, while only sacrificing a small improvement in utility.
6. Use Off-the-Shelf Components
Off-the-shelf components in manufacturing are product pieces that can simply be purchased instead of being crafted entirely from scratch. Incorporating the use of off-the-shelf components into a product’s design can help keep costs down in a variety of ways. Due to the amount of time you eliminate from the crafting process by omitting ready-made pieces, the manufacturing price of your product can drop significantly.
Another cost-related reason for considering the use of off-the-shelf parts for your product is the inherent flexibility they allow for in the development process. Adjusting ready-made pieces to fit a specific form factor is often an easy undertaking. Adapting custom-made pieces to an evolving design can leave you with loads of incompatible parts that will need to be discarded – a pretty costly mistake to make.
Additional Tips
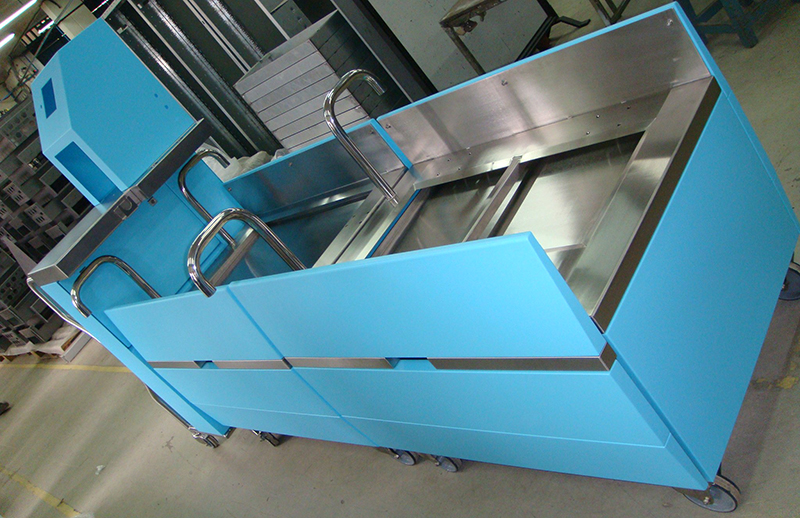
There are a few more ways for you to cut manufacturing costs for your new product or prototype that are worth considering in addition to the others mentioned above.
7. Choose the Right Manufacturer
Merely choosing a manufacturer that works best for your business can help tremendously in keeping costs low. Getting samples beforehand can assist in selecting the right factory for production.
Samples may be a bit costly to acquire from certain factories, but they can help you to decide if the production quality they offer is what you’re looking for before going all-in on a full-sized lot of items.
8. Determine Your Minimum Viable Product
The minimum viable product is a version of your product with the bare necessities needed to get and hold the attention of early consumers. Viewing your product’s design through the lens of a minimum viable product ensures you are not overextending in upfront costs without sure footing in the form of customer expectations.
9. Create a Better Bill of Materials
A bill of materials is essentially a list of everything needed to create your product and the steps taken in the creation process. This document is necessary for serious production purposes and facilitates all stages of development from design to assembly. Improving your bill of materials is likely to come down to encouraging greater collaboration between designers, engineers, and manufacturers.
A poorly designed bill of materials makes for numerous costly mistakes in material sourcing and manufacturing. With all relevant parties actively communicating about and improving the accuracy of the bill of materials, you can avoid the costs well ahead of time.
Cad Crowd Has Freelance Prototype Design Professionals
At Cad Crowd, pre-vetted CAD professionals from around the world can help you with product design services for cost-effective production. All work is handled confidentially between you and your chosen designer. Get in touch to get a free quote on your project.
You can also launch a design contest and receive multiple submissions for your project from all over the world. Learn how you can launch a design contest today!