Iterative design is a tool that goes hand-in-hand with rapid prototyping, but it is very valuable in its own right. The primary goal of iterative design is to create the best product possible with the most ideal function and the fewest number of imperfections and inefficiencies. Rapid prototyping services tend to be used alongside it as a way to evaluate new designs and changes as quickly as possible.
Utilizing iterative design as a strategy makes sense in many cases, especially when the focus is on long-term quality. Due to the possible number of iterations that a design may go through, the process may take longer than some other strategies. However, it is ultimately a cost-efficient shortcut to a high-quality final design.
What Is Iterative Design and How Does It Work?
The process of an iterative design essentially has three basic steps that are repeated in a cyclical fashion until a satisfactory result has been achieved. Let’s begin by examining each step first.
Design
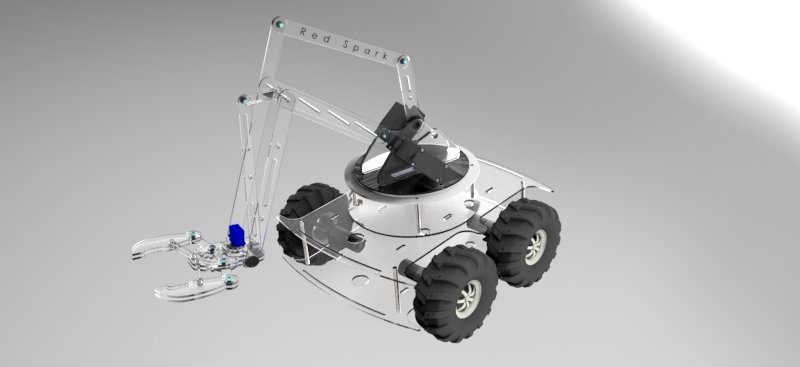
Typically, the cycle begins at the design stage. This is the initial concept. An idea has led to a design for a new product. The quality of this first design is not critically important because of the other steps in the process. It merely serves as a starting point regardless of how similar or different it is to the eventual result.
Prototyping
Of course, once a design has been created, it needs to be tested. There are only so many aspects of a product that can be observed accurately without a physical model. This is where prototyping comes in. Preferences tend to vary when it comes to prototyping. Rapid prototyping offers plenty of advantages, but other methods have unique benefits as well.
Some prefer the more traditional three prototype method, which generally involves proof of concept model, a functional model, and a beta model. In either case, prototypes will be created multiple times.
Evaluation
The evaluation stage is where the new prototype or prototypes are examined very carefully. Assuming that the concept has already been proven, everything else about the prototype is dissected. What could be different? What could be better? Does something need to be added or removed? Is it free of hazards that could harm the end-user? All of these questions and more are useful at this stage.
Repeat
After an initial cycle of CAD design, prototyping, and evaluating, it’s time to take the observations from the evaluation stage and return to the design stage. Changes are made to the design, which leads to new prototypes, and these new prototypes need their evaluations.
The cycle of designing, prototyping, and evaluation is often repeated several times. Each cycle results in a prototype that is better than the one that came before it. It is not uncommon to see this cycle repeated three or more times before production moves forward. There is always room for improvement in the design of a new product, but typically a few iterations are sufficient.
Benefits of Iterative Design
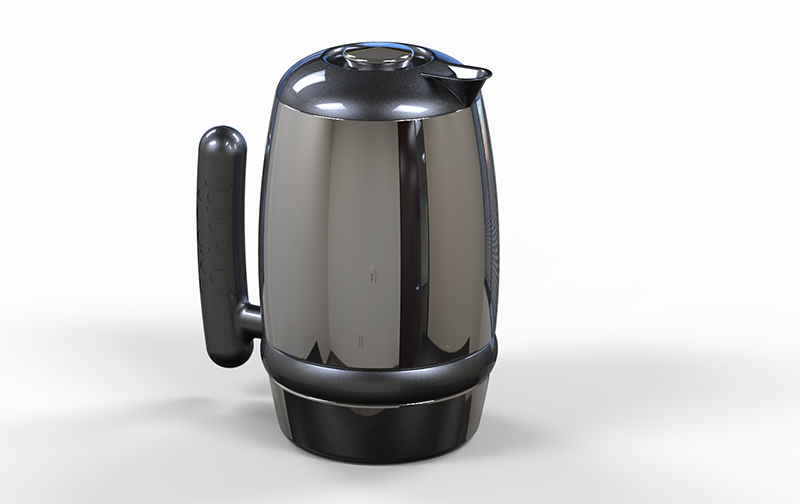
The main goal of iterative design is to produce the best product possible. This kind of thinking brings numerous benefits to businesses that take advantage of it.
1. Final Product Quality
For example, let’s say Company A is using an iterative design process for its newest product. Their focus is on creating a top-quality product that functions as expected time and time again.
The iterative 3D modeling design process may be more costly for Company A during the early stages, but they will ultimately begin full production with a product they can be satisfied with and will likely avoid expensive and disruptive revisions that need to be implemented after the product is already in full production. They’re spending a little more on design and prototyping to avoid far more costly problems later. This benefit alone is tremendous for small and large businesses alike.
2. Damage Control and Reputation Management
Since a large portion of the iterative design process is focused on finding and eliminating problems and undesirable qualities in prototypes, it leaves less room for error in the final product. Businesses that utilize the iterative process are more likely to find flaws themselves while they can still control and correct the situation.
Compared to the alternatives which could be something along the lines of angry customers, loss of market share, or even a product recall, it’s worth the effort to root out the maximum number of imperfections as early as possible. Especially in the case of consumer product design, social media is more significant than ever, and bad news travels fast. It’s tough to put a number on the value of your business’s reputation, but nobody wants to see that theoretical figure decrease.
3. Avoiding Costly Mistakes
This was touched on briefly as part of benefit one, but it’s certainly worth considering on its own. Let’s use large scale production of an intricate product for skilled trade workers as an example. It’s safe to assume that such a product would be made from high quality machined components, maybe some stamped parts from progressive dies, and perhaps a few molded plastic pieces for comfort, aesthetics, or function.
Now, the production of the machined components may or may not require special tooling or fixtures. The progressive dies would be designed for the exact components of the product by a product design service, and the molds would be as well. If you’re familiar with typical rates for machining or specialty tool and die work, then you already know just how quickly the initial costs of these production necessities add up.
Paying for die components, molds, and specialty fixtures once is plenty. Now imagine that all of these necessities are created for a design that is found to be lacking and needs to be replaced with an entirely new design. All of those necessities need to be created again.
The die components, the molds, the fixtures—new versions of each are needed. This can easily cost somewhere in the five-figure range or more depending on complexity and quantities. By utilizing the iterative design process, costly mistakes like these can be minimized or even avoided altogether.
Tips for an Iterative Approach
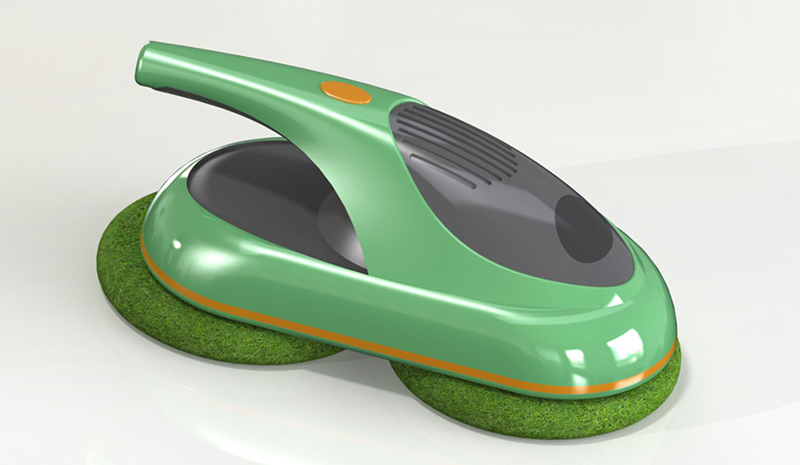
The concept is simple, but there are plenty of small steps that come together to form the complete process. The number one tip to ensure the success of an iterative approach to a new design is to pick the right engineer or designer for the job. Their level of skill is essential, but perspective is also critical with this process. On the subject of perspective, patience is required, but so is a desire to see the project completed in a timely fashion.
Iterative Design Questions and Answers
1. How Many Iterations are Necessary for a High-Quality Final Product?
There isn’t a single, one size fits all answer to this question. Some designs are quite impressive and have little room for improvement from the start. However, this is rare, and most designs benefit from several iterations. Just as a rough number, expect to go through at least three iterations. Three to five iterations are common with new designs. As the process goes on, remember to recognize when good enough is actually good enough to avoid needlessly chasing perfection.
2. Isn’t Iterative Design for Products like Software?
Iterative design is a process, just a series of steps. It is widely used for things like software, but it is very valuable for physical products. New products always have room for improvement over the initial design. The iterative design process provides a logical series of steps for identifying and making those improvements. In short, iterative design is used for a wide variety of products.
3. Are Iterative Design Services Expensive?
This is a matter of perspective. Is it possible that the iterative process may cost more during the development stage of a new product? Yes, it’s possible it may be more costly on the front end. It’s also likely that it will result in large savings once the design is put into full-scale production as opposed to skipping this kind of development. The savings are likely to be found in the form of both time and money.
Definitions
- Iterative Design – Iterative design is a strategy that helps to create the best final design possible. It is a cyclical process that involves three basic steps—design, prototyping, and evaluation. These steps are repeated in succession until the design is satisfactory or further improvements are unwarranted.
- Rapid Prototyping – Rapid prototyping is a process used to create and evaluate realistic prototypes as quickly as possible. Typically, this process relies on three-dimensional design files which are then used for 3D printing.
- Iteration – In the case of iterative design, an iteration is a full round of the process. The cycle of design, prototyping, and evaluation is one iteration. It is common for a new product that is designed with the iterative process to go through several iterations before it is entirely ready for production.
Rates
The exact cost of iterative design can vary wildly due to the simple fact that the stages are likely to involve different professionals. While a fantastic freelance mechanical engineer may be picked for the project, they probably won’t be the one on the shop floor making the parts for the prototype. It’s pretty tough to throw out any exact figures since the number of iterations is also a significant factor, but expect to pay rates that are in line with industry standards across the board.
3D Modeling Software
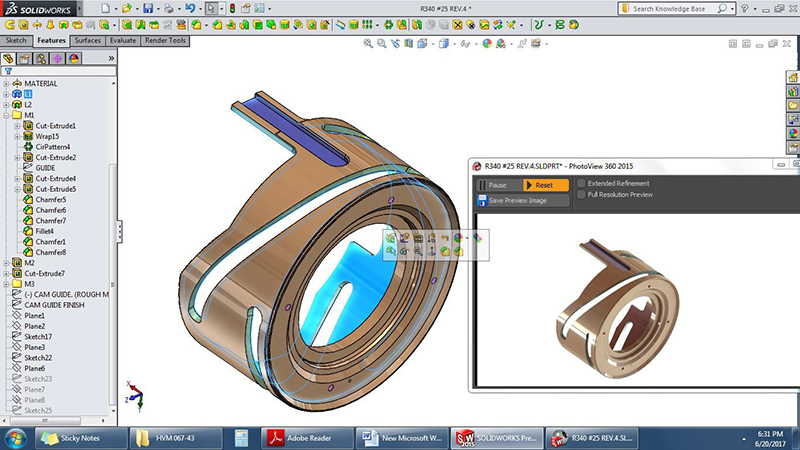
Any 3D modeling software of sufficient capabilities could be used for iterative design. Typically, engineers and 3D design services will use SolidWorks for this. This software allows them to create digital 3D models with incredible levels of detail. SolidWorks is a powerful design program, and working with it can even reveal several design issues before prototypes are created. Some professionals prefer other similar programs, such as Creo or Inventor.
Summary
Iterative design is essentially a simple concept based on sound and reasonable logic. Create a design, build a prototype or multiple prototypes, evaluate the prototypes, then go back to the design to make changes. This process takes a lot of hassle out of creating new products. It’s a short-cut to a high-quality product, and it can be used to avoid numerous costly mistakes.
If you believe that iterative design services are right for you, your business, or your project, then it would be best to find a designer or engineer that is familiar with the process.
Skilled Iterative Design Engineers and Designers
However, finding the right engineer or CAD service for a job can be challenging. Cad Crowd makes this process as simple as possible. There are already a variety of engineers and designers in the Cad Crowd talent pool that are skilled, proven, trusted, and vetted.
There are even standard processes in place to protect your rights as a client and the privacy of your information. Don’t waste time debating about privacy or intellectual property rights, utilize the vetted talent at Cad Crowd, and keep things simple. If you’re ready to start working with an engineer or designer, find out how it works and get a quote today.