Today’s article looks at 3D printed masks and innovative medical device design services for the medical field. Severe trauma is one of the worst and most tragic experiences ever in a child’s life. Unfortunately, accidents can occur in the most unexpected moments. The good news is that there is now an excellent place for recovery for these children, and this is none other than Romans Ferrari.
To make things better, the center has been exploring greater heights as they use 3D printed masks and medical devices made and designed to help their patients heal and recover from their trauma. This article discusses how Romans Ferrari developed a new digital workflow to develop custom compressive masks to treat facial burns with the help of 3D printing and 3D scanning, made possible by the multi-team collaboration among engineering design professionals, prosthetists, and doctors.
RELATED: How to design medical products that people actually want
What is Romans Ferrari?
Romans Ferrari, located near Lyon in France, is a pediatric rehabilitation center offering care to adolescents and children who suffer from trauma, severe burns, polytrauma, brain tumors, and brain damage. The center has extensive experience treating severe facial burns, including using specialized compressive masks that lower the risk of scarring and complications. However, the conventional production method of these masks involves a somewhat uncomfortable workflow that can cause children to have PTSD or post-traumatic stress disorder.
How are severe burns treated?
Romans Ferrari welcomes adolescents and children from different parts of France with referrals from other hospitals following the initial treatments of life-saving and ICU. The initial step is welcoming patients as soon as possible as far as the medical standpoint is concerned to prevent the formation of scarring complications like hypertrophic scars and scar contractures, which mean the development of thick and fibrous scars and volume gains.
RELATED: How design firms use prototypes to develop critical new medical devices
The main objective here is for the wounds to be epidermis as soon as possible to ensure that there won’t be any open wounds that may result in fluid disbalance, complications, and infections. Actual rehabilitation then begins, involving rehabilitation sessions and compressions to dress the skin. The rehabilitation sessions combine filiform showers, physiotherapy, and other methods.
The compression devices allow the maturing and healing of scars to prevent complications, improve the texture of the spot, improve the skin’s flexibility, and guide the body to produce the most aesthetic and comfortable imperfections possible while the patient grows. More than the traditional compressions that burn centers worldwide use today, the medical devices design team at Romans Ferrari also came up with custom devices, including the specialized reliefs that the center refers to as DMDGs or growth and maturation devices.
This allows more targeted support at the level of the scar and a finer means of working on the progression of the spot in terms of intra-scar elasticity and adhesion. Compressive masks for facial burns used to be developed from plaster casts. The orthoprosthetist developed a negative with plaster strips. They created a positive from there and used it for thermoforming the final mask.
RELATED: The faster, easier way to develop new medical devices
While applying the plaster cast lasting approximately one hour, the patients have to stay motionless, which can be tricky, particularly for kids. It might even cause reactive symptoms of PTSD or post-traumatic stress disorder due to the warmth of the bandages. Sometimes, it’s also unpleasant for the patients if heat is applied to their faces.
Digital workflow invention for compressive facial masks
According to Romans Ferrari’s General Manager, Christophe Debat, they have been dreaming of 3D printing services for the longest time. The team had imagined that 3D printers would allow the production of masks according to the scanned file, even without touching the patient. However, the good news is that Mr. Veauville, with an engineering perspective, arrived and was the one who suggested that it’s best to entrust the job to the hands of the engineers.
RELATED: Medical device design: a guide to service pricing, costs, and rates for companies
Romans Ferrari’s board member, Jean-François Veauville, previously worked in Toulouse as an aeronautical construction engineer specializing in composite materials. Veauville gave the engineering students at École Centrale de Lyon a research study, a study they had to complete to understand better the possibility of using 3D printing to produce masks or improve its development process directly.
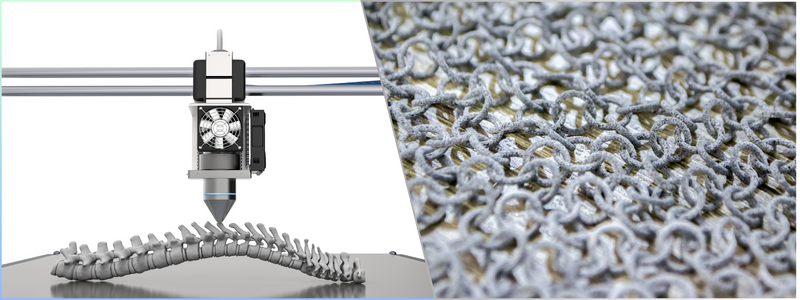
They assessed several available 3D printing technologies and worked hand in hand with the service providers to order test prints. After more than six months of intensive research, they got results that showed the possibility of using 3D printing to produce positives that were once made out of plaster. However, it was only a part of a more significant challenge since the team had to discover a method of digitalizing the workflow.
The student team connected Mr. Veauville with 3DZ France, a 3D printing equipment integrator and reseller. They collaborated with the team at Romans Ferrari to discover the perfect solution for every stage of the workflow. It included the highly accurate digital replication of the existing manual process, identifying the correct 3D printing solution to produce the masks, and validating the workflow.
According to 3DZ France CEO Patrick Ferraris, the real challenge was understanding what the practitioners were trying to express and transforming the medical language to technical language due to the differences in lexicons. The initial challenge was relieving the children while capturing the scanning data. The second challenge is to develop an easy-to-deploy solution that even practitioner-level students can learn immediately.
The latest workflow involves scanning the face of the patient using a 3D scanner and then using CAD design professionals to create the mask according to the scan. Before scanning, the doctor will carefully mark the DMDC devices’ locations on the patient’s face. Meanwhile, the technician will use a digital pen to add the engraved details into the design precisely. The mask will be 3D printed using Fuse 1 SLS or selective laser sintering 3D printer and act as the positive to thermoform the final show.
Mr. Veauville stated that since it’s expensive to subcontract the masks and take a few days, Romans Ferrari was trying to find a 3D printing solution that they could directly implement in the center. The facility’s health agency needs to compensate for this kind of development. Thanks to donations, the center could work on it, and since the machine recommended to them was reasonably priced, it fit their budget.
RELATED: Designing new medical products & devices: a step-by-step guide for your company
3D printing services for better results and enhanced comfort for the patient
The latest workflow that involves 3D printing is noticeably faster and much more comfortable for patients since their faces are no longer covered in plaster strips. 3D printing has also been offering satisfactory results. However, the team had to work together and provide training to orthoprosthetists regarding the sufficiently precise placement of DMDG devices. It’s essential to put these reliefs of various shapes on the scar in a very exact way depending on the zones that require it.
Patients usually stay for over a year in the center, depending on how severe their injuries are and the required rehabilitation. Throughout this period, they reside on the site and continue their studies. They even attend concerts, go on group outings, and prepare for the outside life since, at first, it might be challenging to do so without constantly worrying about others looking at them. Romans Ferrari treats around 25% of French children suffering from severe burns.
RELATED: How the healthcare industry uses 3D printing and 3D bioprinting for treating patients
The center has also worked with other clinics across France and countries, including Jordan and Italy. Thanks to the rise of digital technologies, including 3D printing and 3D scanning services, offering treatment for patients living outside Lyon has become more possible. Not too long ago, Romans Ferrari worked with Doctors Without Borders in Jordan. The doctors scanned the patient’s face, and the scan file was sent to the pediatric rehabilitation center.
The team developed compressive devices in France that were later shipped to Jordan. Thanks to the extensive experience of Romans Ferrari, they have made it their goal to offer and use this strategy to all the patients because the tools and methods they produce are not unique but more efficient than those currently available elsewhere. Their next goal is to look for partners with whom they will have the scanner and a doctor in charge of designing the medical devices. They will then manufacture them at a cost to ensure that other patients can also enjoy this state-of-the-art innovation’s perks.
RELATED: 6 Ways 3D printing will change the world
How Cad Crowd can help
Burn and severe trauma patients deserve the best care to help them continue with their lives. Cad Crowd is a platform where you can find experts who can design 3D-printed masks and medical devices to help heal scars and wounds inside and out.