An effective medical prototype design possesses specific vital attributes: they are suitable for its intended use, adheres to healthcare regulations, and be user-friendly. Everything sounds simple enough, but the actual design process is much more challenging than it appears to be. Medical devices are products meant to diagnose, cure, treat, mitigate, or prevent diseases. They can’t rely on chemical reactions or the metabolism system. Even a minor design flaw can pose serious health risks.
The FDA classifies medical devices in 3 categories. Class I includes low-risk medical devices that can be self-registered, such as bandages and face masks. Class II indicates moderate to high-risk profiles, such as syringes and powered wheelchairs. The category accounts for more than 40% of all medical devices in the market. Class III is for invasive and potentially dangerous devices like pacemakers and implants. FDA’s approval requirements are more complex, lengthy, and expensive for higher-risk devices.
Major medical prototype design factors
Much like other products, medical devices must undergo a design development process before making it available. But unlike typical home appliances, the prototyping stages of Class II and Class III categories can present monumental challenges and require massive financial resources. Major design factors when developing a medical device prototype design are as follows.
Cost of medical prototype design
A prototype does not come out of thin air. Before any design can be built into a prototype form, it must go through multiple design, engineering, and documentation phases. From the earliest build model to the beta (nearly production ready) version, a medium complexity Class II medical device costs around $2 – 5 million, approximately 10% of the total product development budget. Class III medical prototype may cost tens of millions, whereas the lowest-risk Class I would require no more than $200,000 depending on complexity.
The amount does not include the cost of FDA submission and approval, certifications for health and safety, mass production, and IP-related matters. Much money is allocated towards market research, clinical trials, and ongoing CAD modeling and improvements.
Medical device prototyping occurs in multiple steps. An early prototype is meant to represent the primary form of the product, whereas the late-stage model is supposed to work as intended and be ready for clinical tests. The process involves a lot of money, so make sure each round of prototyping delivers quality functional products.
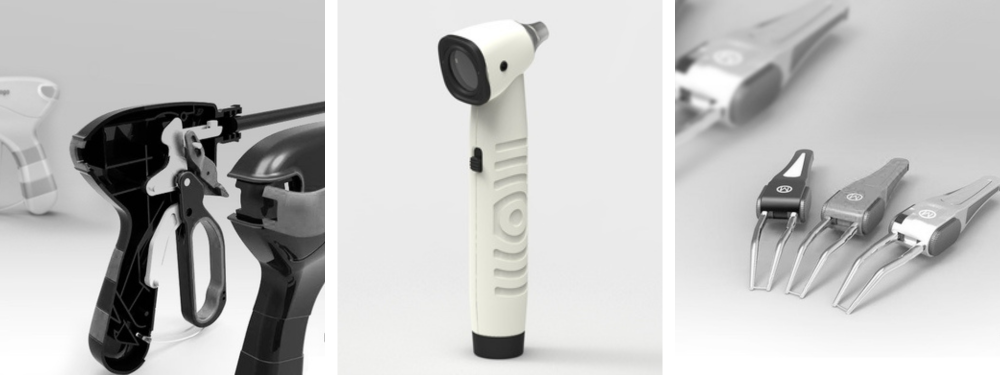
RELATED: Designing new medical products & devices: a step-by-step guide for your company
Material selection
Performance requirements and end-use applications are the primary consideration when deciding what materials to use for the device and its components. The same principle applies to all products and is indispensable when designing invasive medical devices like pacemakers, implants, and prostheses. Some machines must be made from biocompatible materials yet as durable as its intended life cycle.
Only some prototypes require end-use materials, especially if those are hard to come by. Early models usually focus on appearance and form factors and can be constructed from affordable materials such as resin or aluminum alloy.
Early models include:
- Appearance prototype: a simple physical mock-up, possibly 3D printed or made from foam board. The model is intended to “only” look like the final product and is barely functional beyond providing references to product dimensions, ergonomics, and visual features. If you decide to utilize 3D printing design services instead of manual handcrafting, you must first create a photorealistic 3D model of the design. The cost for detailed 3D modeling is around $15,000; the printing process costs around $500 to $1000 for high-quality results. Price also depends on size and materials.
- Proof of Concept: a more sophisticated version of the appearance model and is used for component feasibility evaluation. A proof-of-concept should demonstrate the device’s primary user interface and that everything can be manufactured using existing technology. Building such a prototype with 3D printing is still possible despite the added complexity.
As the development moves forward to the “functional” phase, including alpha and beta models, the prototyping process likely requires a combination of 3D printing and CNC machining for accuracy. If the device consists of multiple mechanical and electronic parts, there must be separate prototyping processes for the PCB (printed circuit board) and the enclosure. The PCB design/layout and prototype cost $5,000 to $20,000; the CNC machining rate varies from $30 to $50 per hour including the raw materials.
Manufacturing technology
Most medical devices, especially Class II and Class III are complex assemblies with many intricate components made from various advanced materials. Except for the Class I category, nearly all of them are built using at least two manufacturing methods: rapid prototyping and CNC machining. You will not need injection molding, which is usually for mass-production purposes.
Both CNC machining and 3D printing offer good accuracy. The former can work with various metal materials, whereas the latter is more suitable for plastic parts. The primary advantage of 3D printing is the rapid production of intricate design components and geometries, including internal cavities. The printing can begin just as soon as the CAD file is ready. While CNC machining can also build a similar shape, it requires a more complex setup process, tooling, and programming.
You can usually outsource 3D printing and freelance CNC machine design experts to a prototyping firm. Instead of making a massive investment in the latest manufacturing technology and operators’ training, hiring an external party to do the job is more cost-efficient. There is an abundance of local prototype makers, so it is optional to outsource overseas.
Bear in mind that the cost of a prototype always consists of two parts: the engineering cost to design the device and the actual price to build it. A biomedical engineer is the most competent professional to help you design and build a prototype of a Class II or Class III medical device.
For the Class I category, you don’t necessarily need someone with a medical background to design the device. Based on data from the BLS, the median annual wage for a biomedical engineer is $97,410 or around $46.8 hourly rate. Assuming your device takes two years to develop into a beta prototype, the salary is nearly $195,000 per engineer.
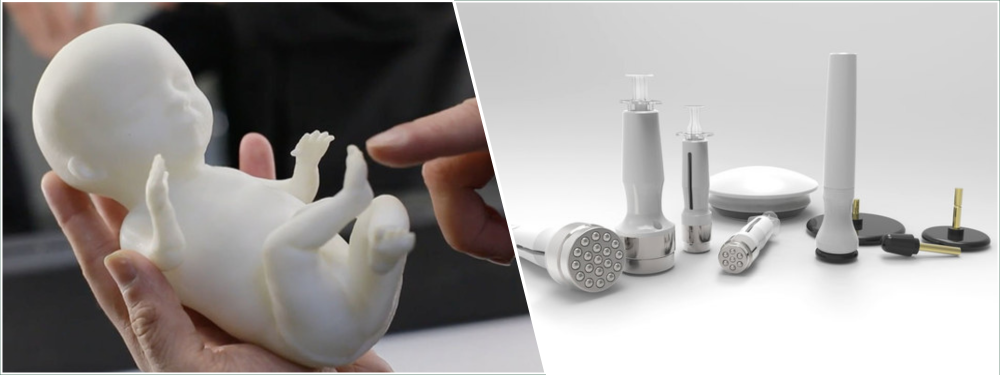
Save money on medical prototype design
Building a prototype takes a considerable investment of time and money. Still, it allows you to make all the necessary adjustments to dimension, design, materials, features, form factor, and functionality early in development. You can ignore the prototyping task and go directly to mass production based on a CAD model.
However, such an approach is a gross waste of resources because the end product will inevitably require plenty of adjustments. It would be best to have several prototype iterations, each with a small production volume. The process consumes more financial resources as the development approaches the beta or final prototype stage. However, there are some practical ways to keep it efficient.
Design for manufacturing (DFM) principles
During the design phase, Design for Assembly (DFA) services aim to decrease the cost and difficulty of assembly, while Design for Manufacturing (DFM) services prioritize technical feasibility and low production cost. One of the critical principles of DFM is selecting appropriate materials, as each component affects the final cost and quality of the product. Every material has unique mechanical properties, such as flammability, thermal efficiency, conductance, and rust resistance, impacting manufacturability and device functionality.
Component design plays a massive factor in manufacturing methods and cost. For example, it is possible to use plastic material of varying thickness for the device enclosure as long as it doesn’t affect its strength. However, DFM analysis revealed that uniform thickness is a more feasible choice to save money in prototyping, whether with 3D printing, CNC machining, or injection molding methods. DFM tools and analysis empowers engineers to build cost-effective design without compromising features, durability, or functionality.
Modern software for a medical prototype design
Product design presented as a three-dimensional model offers better visualization than the traditional 2D diagram. In addition to 3D CAD for modeling and rapid prototyping purposes, engineers may utilize other modern programs like computational fluid dynamics simulation and cloud computing for design collaboration. Cloud computing allows engineers to update and improve ideas in a single design database environment while avoiding cumbersome individual record-keeping when used as a collaborative tool.
When combined with software tools to analyze material performance under pressure and general usage simulation, engineers can see how the product should perform even before prototyping begins. Data from the digital test can be used as the basis for preliminary reviews and refinements. The real-world test remains irreplaceable, but at least digital simulation can help reduce unnecessary mistakes.
Feature creep elimination
Added features—or functions beyond the core design requirements—add to the prototyping complexity and cost. Aesthetic considerations are added features, but in most cases, such visual appeal is necessary only for a competitive edge in the market. For example, some medical devices require a mirror or high-polish finish for cleanliness, but most healthcare equipment works perfectly fine without a shiny surface. If certain features are unnecessary, it is best to exclude them from the design to simplify the prototyping complexity and reduce cost.
How Cad Crowd can assist
Are you ready to navigate the world of medical prototype design with a clearer understanding of the costs, rates, and pricing involved? Get in touch with our expert team at Cad Crowd today. With a global network of professional designers and engineers experienced in the medical field, we can provide customized solutions that fit your budget. Request a free quote now and take the first step towards bringing your medical innovation to life!
RELATED: How design firms use prototypes to develop critical new medical devices