A large part of product design and development is allocated for prototyping, including tasks from ideation to a near-finished design. Once the final prototype is ready, the next step involves mostly minor modifications for manufacturing optimization. Previously, a company probably had to build more than several physical prototypes to analyze and test ideas. The advent of 3D CAD technology, and by extension, computer-generated 3D product modeling, has changed the landscape of product development.
3D product modeling design firms and engineers can replace physical prototypes with geometrically accurate, lifelike digital 3D models. Advanced 3D CAD software can also run a 3D model through virtual simulations to evaluate performance. The simulations generate data about how the design or product will respond to environmental factors, including exposure to water, extreme heat, heavy usage, and common wear and tear.
Using software tools to create a digital 3D representation of an object is known as 3D modeling. Like any other computer program, the 3D CAD and 3D product modeling process is built on the foundation of complex mathematical formulas instead of an artistic approach. The computer does the calculations, and users operate the more intuitive graphical interface. 3D product modeling comes in three major types:
RELATED: Accessible design: better products for everyone
Wireframe
An approach to 3D modeling that utilizes interconnecting lines. A digital wireframe object is a skeletal description of an object comprised of only lines, points, and curves to define its edges. The shapes are not filled with solid colors, so the structure is a transparent object with no surface. A complex 3D model is time-consuming since each shape that makes up the wireframe object must be individually drawn and independently positioned. Depending on the viewing angle, you see the front-facing portion of it and every other side.
Surface
As the name implies, the focus is on the outermost layer of the object. It is more detailed than a wireframe because the layer is made of organic shapes, possibly textured or colored. A 3D model of this type defines both the edges and surfaces, so it resembles a physical object instead of appearing as a skeletal structure. The 3D model is hollow, and it has no volume.
RELATED: How-to guide: new product design, engineering and prototyping your idea for mass manufacturing
Solid
The object is created by combining a range of basic 3D shapes, such as cones, boxes, spheres, cylinders, prisms, pyramids, and tori, among others. You build an object by subtracting, joining, and intersecting the shapes. 3D solid modeling is by far the most popular type, as it fits the needs of most product designers. The final 3D solid model may function as a single object or an assembly of multiple 3D components. 3D solid modeling is the easiest yet most capable and detailed. Two 3D modelers can use different techniques to build the same 3D object.
One of the most common techniques is polygonal modeling, which involves polygonal modeling designers creating a mesh of polygons (usually triangles) and manipulating them to form a 3D object. The polygons can be split or deformed to achieve the desired shape. Another popular technique is based on NURBS (Non-Uniform Rational B-splines) mathematical model. NURBS-based modeling has no concept of polygons. If the 3D model has complex curves, NURBS can reach the level of detail that is otherwise impossible with polygonal modeling.
RELATED: Guide to prototyping methods used in product development services for companies and firms
3D sculpting services provide a more straightforward technique. You start with a big block of a 3D object and begin deforming it to build the desired object. 3D sculpting treats the block like clay so you can manipulate it freely. The technique is best for creating organic shapes or natural objects like animals, plants, and even humans. However, the best technique to use for 3D product modeling purposes is 3D CAD (computer-aided design). In some cases, the terms 3D CAD and 3D modeling can be used interchangeably, but there is an important distinction. 3D CAD software builds a model in 3D and creates 2D schematics for an object.
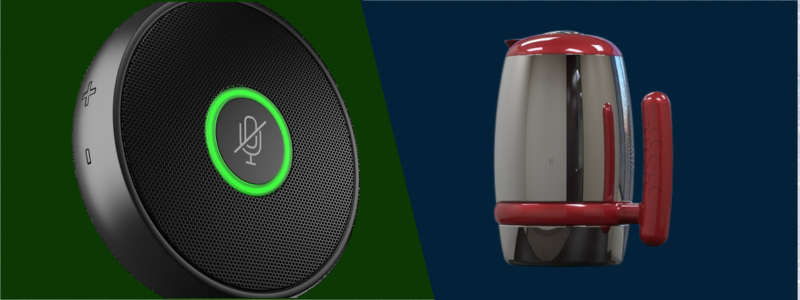
Both the 3D model and the schematics are used for design editing and, eventually, manufacturing data. 3D CAD software aims not only to create a realistic representation of a product but also to generate accurate geometrical data for every component that makes up the object. In other words, a 3D CAD model is a technical design drawing that functions as a virtual prototype and as a database for manufacturing purposes. The 3D model is possibly attached with a specification sheet, such as the materials used for each component and their physical properties or characteristics.
RELATED: The product development process explained in 3 stages
When the 3D model is run through simulation, the parameters (water pressure, air pressure, temperature, impact with other objects, and prolonged use, to name a few) should affect it accordingly. Most types of 3D modeling services are primarily used for artistic and entertainment purposes, but 3D CAD finds its most extensive applications in technical design and manufacturing industries.
3D CAD: 3D product modeling services
Product development is complex, demanding, and likely a resource hog. However, product development is easier with the help of a 3D CAD or 3D product modeling professional. A virtual model helps a company envision a product in detail; it is more comprehensive than 2D images. A digital yet realistic product visualization empowers the design team to be more creative and experimental without excessive investment in every iteration of physical prototypes.
RELATED: New product development and design: should your company work with a product design team?
In an ideal world, every company has its own in-house 3D product modeling division as part of the engineering or 3D design department. Each time an idea comes up for a new product, a team of 3D modelers fire up their 3D CAD software and begin digitally visualizing the concept. However, not every company—especially startups and small businesses—can afford to hire a group of full-time 3D CAD design experts. Since no company should design a new product daily, outsourcing the 3D product modeling work to freelancers often makes more financial sense. Even among big companies, the decision to outsource is often triggered by economic reasons. Hiring an external firm or an individual freelancer to handle 3D product modeling is more budget-friendly than keeping 3D CAD modelers on the payroll.
A typical workflow of 3D product modeling service is as follows:
- Project brief: clients submit the project brief, filled with as much information as possible about the design. Most professionals will encourage you to include a 2D concept (hand-drawn) visualization as a reference. It is better to go back and forth during the early stage rather than revise the 3D product model multiple times later.
- Concept art: some 3D modeling services are willing to create concept art for any product. The concepts are preliminary deliverables, allowing the client to determine the best design.
- 3D modeling: after the client refines the brief or picks a specific design from the provided concepts, the actual 3D modeling process begins. Depending on the brief, the 3D model can be strictly technical without additional superficial details like textures and branding. If the product is an assembly of various parts, each component might be color-coded for clarity.
- Optimization: the finished 3D models are sent to the client for review. The 3D models can be revised and optimized as necessary.
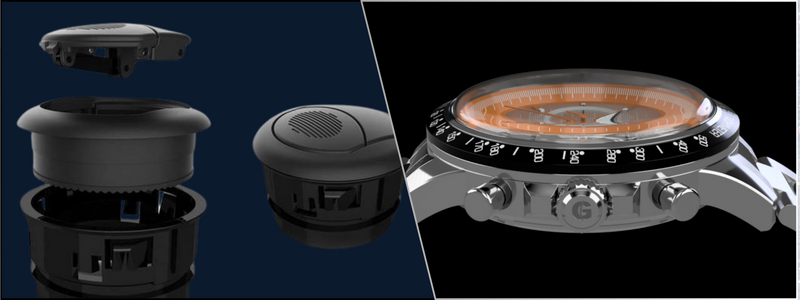
RELATED: 10 Tips for hiring a freelance 3D modeler
3D modeling is not to be mistaken for 3D rendering firms. The final deliverable in a 3D modeling project is a 3D file that contains technical data about the product/object. A 3D file can be further modified, whether the specification or structure, in 3D CAD software. The file is not a rendered 2D image. Many 3D modelers also offer 3D rendering services, which will transform the asset into an image format. 3D rendering is usually the last step in a product visualization project after the design is approved and ready for manufacturing; it does not require further modification. The images are used primarily for marketing purposes.
Cost
You can get the best prices from freelancing marketplaces for outsourced 3D product modeling projects. The freelance portals consistently have unmatchable rates, but there is due diligence to do on your part. While many of them are experienced professionals, others are not as qualified. On average, the hourly rate for 3D product modeling freelancers is $40/hour. The inexperienced 3D CAD product modeling providers will likely charge less (between $15 and $25). It is not uncommon for skillful 3D modelers to rate the services at $50 to $100 per hour.
RELATED: 3D Modeling: an overview of history & industry applications
Depending on the product design and complexity, hiring professionals on a per-project basis may make more sense. A 3D model of a complicated mechanical product with plenty of moving parts is more challenging than a virtual prototype of a simple cube or a box of chocolate. Many complex products cannot be 3D modeled within a day, so per-project pricing can save your firm money. Flat rate pricing per project varies from $400 to $5000 depending on complexity. Most freelance 3D modelers calculate the price based on the days required to finish the model; each full working day is typically $400 to $500.
If a product is simple enough that the 3D modeler can get it done within a day, the hourly rate pricing structure is the economical option. A complex mechanical part of an automobile may require a week or more to finish, so a per-project method is preferable, although the rate is still based on the 3D modeler’s daily rate.
RELATED: Pros and cons of hiring a freelance 3D modeler
Here is a table summarizing the information about pricing options for outsourced 3D product modeling projects:
Pricing Method | Average Rate | Range of Rates | Suitable for |
---|---|---|---|
Hourly Rate | $40/hour | $15 to $100/hour | Simple and quick projects |
Per-Project (Flat Fee) | $400 to $5000 | Varies based on complexity | Complex and time-consuming projects |
Daily Rate (Per Project) | $400 to $500 per working day | Varies based on complexity | Complex projects that may take several days |
Remember that the suitability of each pricing method depends on the complexity and timeline of your 3D product modeling project. Hourly rates are economical for simple, quick projects, while per-project and daily rate pricing structures are more suitable for complex projects that may take longer to complete. Additionally, it’s important to exercise due diligence when selecting freelancers to ensure they are qualified for your specific project.
How Cad Crowd can assist
At Cad Crowd, we have the privilege of working with hundreds of freelance product designers and 3D modeling services. If you’d like to get professional help, contact us today for a free quote.