Gone are the days when 3D printing was merely a tool for rapid prototyping for the automotive industry. With all the modern advancements in AM or additive manufacturing, today’s automakers are starting to incorporate 3D-printed cars and innovative services as part of their production processes.
Customization in modern automotive manufacturing
As modern manufacturing leans much further to mass customization, it’s necessary for automotive OEMs to continuously search for ways to develop vehicles specifically tailored to the customers’ needs. 3D printing is a flexible and cost-effective way of producing customized parts. Companies in the motorsports and luxury segment of the industry already use the technology for the production of personalized parts for the exterior and interior features of the vehicle. Offering customers customization options is one of the ways that automakers try to enhance customers’ experience and boost their competitive edge.
Luxury vehicles are a particular automotive industry segment that uses 3D printing design services for customization. In this segment, where it’s normal to have small production runs, it’s possible to use 3D printing to create parts that are tailored to specific customer requirements in a shorter timeframe. Printing has the potential to transform the stage of product design, with customers now given a better say in the appearance of their vehicles.
RELATED: Automotive design & engineering services, costs, rates pricing for companies
Design innovation using 3D printing
It’s also possible to use 3D printing to create intricate and complex designs that would have been impossible with traditional manufacturing methods. It is a particularly beneficial capability when developing customized functional parts. Since weight area is a critical concern for automotive OEMs, with lighter vehicles often having lower fuel consumption, the design engineers can also utilize 3D printing with tools such as generative design and topology optimization. These can remove material in certain areas and develop parts with optimized performance and weight.
Simplified assembly with 3D printing
One way automotive OEMs can take advantage of 3D printing. Since traditional manufacturing methods don’t offer the same design freedom that 3D printing can offer, several components should be typically produced to develop a final piece. Regarding part consolidation, several parts of the component can be incorporated into one piece during the design stage.
Consolidated design can usually only be produced by an experienced product design company through 3D printing thanks to its complexity. Using this approach, 3D printing simplifies the assembly process by reducing the components required at the assembly stage. Rising above the need for various parts helps reduce assembly costs, time, and material usage.
RELATED: CAD automotive design – when driving becomes personal
What 3D printing materials are used for automotive applications?
Most automotive applications need materials that mix flexibility and toughness with chemical and heat resistance. 3D printing using high-strength polymers such as PEEK and nylon, metals such as titanium, steel alloys, and aluminum, and plastics like ABS or ASA are some of the most common choices for producing functional tooling and car components. Using carbon fiber companies with 3D printing is also possible, which opens a new door to producing even lighter car parts.
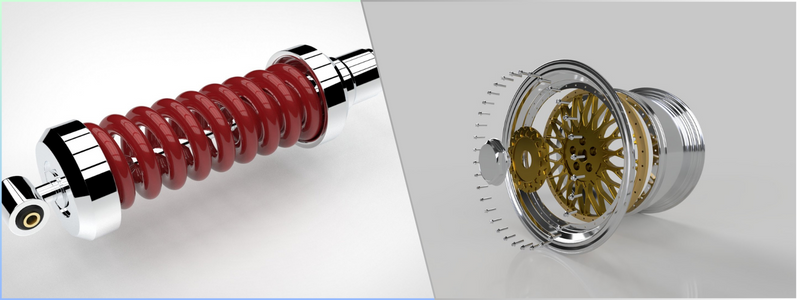
How to integrate 3D printing into the process of automotive production
Product validation and development
Since it’s possible to produce multiple iterations of the design within a short period at a very minimal additional cost, 3D printing is considered an effective product development tool. A part must typically undergo several design cycles before agreeing upon the final design. This phase can speed up dramatically with 3F printing. In addition, cost-efficient improvements in design can be developed relatively fast because the technology doesn’t require pricey tooling for prototype production.
Currently, the use of 3D printing for performance validation, testing, and prototyping design services is among the most famous applications of this technology in the automotive industry. The low costs of production that 3D printing allows means that design engineers will be able to check the function and fit of a component before they invest in expensive and often labor-intensive molds for the end-part production.
RELATED: Get your engine revving: 5 automotive CAD designs
A good example here is tail-light covers. The prototypes of such parts are typically produced using molding or milling. The primary challenge with such production techniques is that the tail-light housing’s multicolored covers should be made separately and assembled afterward. It lengthens lead times for verification of the design and delays time to market as a result.
Tooling
Although prototyping remains the main application of 3D printing in the automotive industry, technology’s use for tooling is quickly catching on. The use of this technology for this specific application offers a lot of benefits. The tooling production internally lowers the costs of tool production for the car maker by up to 90% and reduces lead times from weeks to only a matter of days.
As far as manufacturing aids are concerned, 3D printing is quickly becoming a substitute for more established manufacturing tools. Within a few years or so, it’s likely to see more and more automotive OEMs turning to 3D-printing tooling to enhance production efficiency and tool performance.
RELATED: What is 3D printing? A beginner’s guide
Spare parts
Automotive design professionals can also leverage the perks of 3D printing to produce spare parts on demand. Due to the high inventory costs in terms of storing sparse and usually rarely ordered components, 3D printing offers a cost-effective way to develop features required on demand and on time, resulting in better delivery times, lower costs of inventory, and a more simplified supply chain.
End-part production
The latest AM materials and technology advancements unlocked 3D printing to develop medium- and small-use end-use parts. Industry experts envision that 3D printing will aid in producing end-use car parts. These 3D-printed end-use automotive parts can vary from inner parts to exterior components such as engine components, mounting brackets, complex ducting, and bellows.
3D printing and motorsports
Using AM as a competitive edge for developing race cars has become a standard practice. 3D printing in motorsports has become an integral tool for producing accurate and durable parts for wind tunnel testing. Testing is another advantage. If there is a need to change the design, AM will make it easier to develop components faster, which can then undergo testing in the wind tunnel. Most race car teams are exploring 3D printing to produce end-use car components.
RELATED: 6 Ways 3D printing will change the world
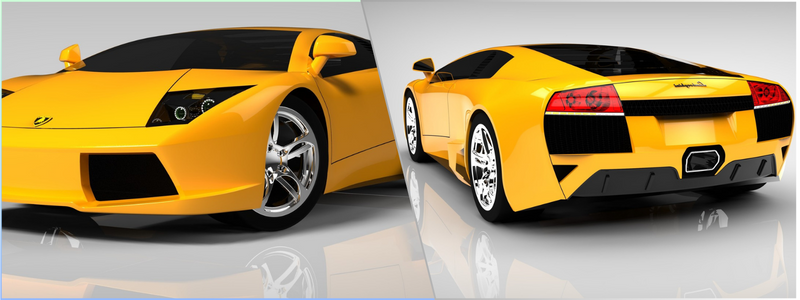
Challenges of 3D printing in the automotive industry
AM skills gap
Extra investment in developing AM-specific skills should be addressed for the 3D printing technology to spread its wings fully. Design for AM and the maintenance and operation of AM materials, post-processing, and materials are all critical skills that require development and nurturing. Although a lot has already been said about the current AM skills gap, partnerships with internal training programs and universities are a great way to ensure a more skilled talent pool with the ability to work with AM technology and its particularities.
Build sizes
Automakers also need help with the limited build size of most AM systems. Even though it’s possible to produce more extensive parts using 3D printing technology, it should be done through modular parts. These must be attached or assembled through other processes like welding. However, large-scale design for additive manufacturing services is a growing and critical research field with technologies that support bigger build sizes that undergo active research and development.
RELATED: Top 101 engineering and mechanical design firms in the United States
Mass production
Although automotive OEMs are starting to incorporate AM systems into production and development, another challenge is production volumes that hinder broader adoption. With more than 92 million cars that rolled out in 2019 alone, today’s automotive industry relies heavily on mass series production. 3D printing, at its present stage, can’t produce parts at the speed and volume that the automotive industry requires. Therefore, the technology should serve as a substitute for traditional manufacturing methods suitable for mass volumes. Instead, it should only be a complementary tool for customized lower-volume production.
Manufacturing firms that utilize 3D printing hardware are also coming up with methods for higher volume production to cater to the automotive industry’s needs. Metal binder jetting is an excellent example of this and was developed by Desktop Metal, GE Additive, ExOne, and HP. Aside from metal binder jetting, the 3D printers can also use powdered materials like sand, ceramics, and plastic, as well as a bonding agent, to quickly produce a part one layer after another operating data from the digital design file.
RELATED: Cad Crowd’s Automobile Design Freelancers are Top Notch
Unlike 3D printers that use an electron or laser beam and produce a part or two simultaneously, binder jetting machines, for instance, can have dozens of brackets in one go thanks to the larger printing area while building up the layers much faster.
How Cad Crowd can help
With automakers continuously searching for new 3D printing applications, this technology is gaining traction. Cad Crowd is the best place to search for professionals skilled in 3D printing and similar innovative services. Contact us for a free quote.