The beauty of eyewear is that users can personalize it according to functionality and personal style. Eyewear makers can adjust different elements, from the thickness of the lenses to the specific material used. Now that 3D printing design services has become more advanced than ever in finishing processes, material versatility, accuracy, and resolution, the state-of-the-art technology offers a cost-effective way for eyewear design and manufacturing. This guide explores 3D-printed glasses and eyewear services and how they transform the eyewear industry.
The rise of 3D-printed glasses and eyewear services
The past five years have seen the adoption of end-use 3D printed eyewear as both more prominent brands and smaller companies make the most out of the production of smaller batches, the freedom of design, and the sustainability benefits of 3D printing. Whether for functional performance, workplace protection, or fashion purposes, 3D printing has found its way to the eyewear industry and transformed how manufacturers and designers think about and plan production.
RELATED: What is 3D printing? A beginner’s guide
One of the most significant advantages of hiring 3D printing designers is the reduced number of steps for assembly during manufacturing while retaining a high level of product quality and consistency. Several eyewear makers stated that up to 60 individual steps are involved in producing acetate frames alone. SLS or selective laser sintering 3D printing is the most popular technology for additive manufacturing used for industrial applications that manufacturers and engineers from various industries trust and rely on thanks to its ability to produce functional and robust parts.
SLS 3D printers have a high-powered laser for fusing the polymer powder’s small particles. This unfused powder supports the part throughout the printing and eliminates the need for dedicated support structures. SLS is recommended for complex geometries such as negative features, thin walls, undercuts, and interior features. Parts developed with SLS printing have outstanding mechanical characteristics whose strength is similar to the injection molded parts. This makes the process perfect for the production of 3D-printed glasses and eyewear.
RELATED: 6 Ways 3D printing will change the world
Benefits of 3D printed glasses and eyewear services
Here are the top reasons why you should consider using 3D-printed glasses and eyewear services:
1. Establish your brand
With 3D printing, you can stay ahead of your competitors as you enjoy a more efficient manufacturing process. Using design for additive manufacturing companies is also ideal for establishing your DNA and brand. 3D printing combines innovation and aesthetics that help push your company to a new level.
2. Personalization and customization
Product personalization and customization are now within reach without minimum order quantities and tooling requirements. This enables custom design and sizing options to give customers a better fitting or unique product. It’s already been a while since 3D printing has been used to allow product customization in different fields, including audiology, action figures, and orthotics. It often enjoys the most success when the customers feel the product is elevated to become more personally appealing and functional.
RELATED: 3D Printed threads and screws: innovative product design options for companies
As the world is filled with different facial features, ethnicities, and ages, product designers are also shying away from the aged mentality of one size fits all, pushing them further into the world of personalization and customization. 3D printing allows everything to be done in a snap of a finger. If you’re already familiar with CAD design, adjusting the 3D model can be quickly done. It can then be uploaded to the software and printed directly. This differs from milling, which requires expensive and individual tool development for holding the elements in the machine.
3. Freedom of design
Unlike other polymers’ 3D printing technology, the parts developed using SLS 3D printing don’t need support structures. This is because the surrounding powder bed supports them instead. Without sprues, support structures, or restrictions on undercuts and draft angles joints in traditional cutting or molding processes, SLS 3D printing provides almost unlimited freedom in design, allowing advanced methods that used to be too expensive or even downright impossible to develop.
RELATED: 3D Printing with metals: making fully metal parts and products with additive manufacturing
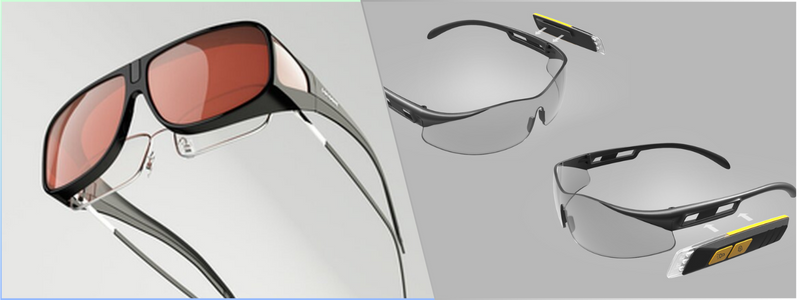
Restrictions in manufacturing no longer hinder product modeling design firms from producing the best-fitting, most fashionable, and most functional designs. 3D-printed glasses and eyewear also allow faster responsiveness to consumer trends than ever before, giving brands a chance to capture emerging new segments in the market.
4. Produce glasses of higher quality
The three primary elements considered when shopping for glasses are the material’s durability, resistance, and quality. Polyamide 12, called Nylon, is typically used for 3D printing glass frames to create similar quality glasses. The material has all the expected properties as it is durable, resistant, and provides excellent design freedom. With the help of 3D printing, you can develop top-quality 3D-printed glasses. Right now, companies are only 3D printing frames. Sooner or later, however, it might even become feasible for glass lenses to be 3D printed as well.
RELATED: 3D Printing technologies for modeling and prototyping
5. Sustainability in manufacturing
The current production of eyewear frames is mainly achieved through precision CNC milling, die cutting, or injection molding services. It forces manufacturers to allot investments in significant equipment and mold costs. However, outsourcing the production of machined parts or molds can cost thousands of dollars and take weeks. To compensate for this expense, the eyewear manufacturers have no choice but to stick with vast numbers of the product, which can lead to high volumes of unsellable stock and lower profits.
Unfortunately, this system is not sustainable for your finances and the environment. 3D printing allows companies to own their manufacturing without mold investment, substantially reducing the risk of rolling out a new line of products. In-house 3D printing can help free manufacturers from committing to unpopular product designs and high MOQ requirements as it allows the production of smaller on-demand batches without upfront costs for molding.
RELATED: How companies use 3D rendering and 3D printing services to reduce material waste
Many eyewear prices right now are developed through a subtractive process or injection molding where acetate gets cut into the selected shape. Cutting requires large acetate sheets and cuts away the frame’s body, with the resulting material ending up as waste. Manufacturing professionals using 3D printing, on the other hand, involves an additive process, which means that the parts are developed one layer after another from a base material supply. It allows recycling the unused powder material and reusing it in the next print, resulting in minimal to no wasted material.
The affordable price point and small footprint allow manufacturers to buy several machines for several locations. It produces a capacity of production in regions that are already physically near the consumers. It also lessens the reliance on the typical overseas production that complications in the global supply chain often slow down. This distributed production can also lower the adverse environmental effects of shipping and overproduction.
RELATED: 3D Printing services, cost and rates for companies and firms
Companies that use 3D printing technologies
Several companies are now harnessing the power of 3D printing technologies. These include the following:
Boulton Eyewear
3D printing technology is a significant part of the business process of Boulton Eyewear. This uses an upgraded version of Digital Light Processing or DLP printing technology that uses less material through customized production. This lowers the costs and results in less waste as well.
Mykita Mylon
It was way back in 2012 when the eyewear industry first welcomed customized 3D-printed glasses. Mykita Mylon was among the first eyewear makers that used 3D printing to produce spectacle frames. The company started exploring polyamide materials in 2007 and using Selective Laser Sintering or SLS to adjust them to the wearer’s facial structure. The company has also won numerous accolades thanks to its frame’s durable and lightweight nature aside from its innovation alone.
RELATED: Why businesses should consider 3D printing services and prototyping for product design
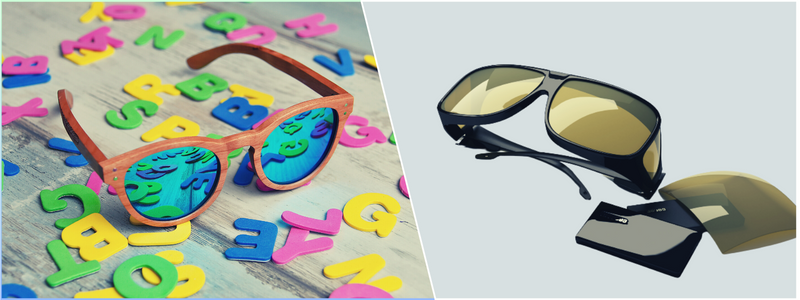
Are there downsides to 3D-printed glasses and eyewear services?
Overall, it might be safe to say that 3D printing is a game-changer. But, finding and owning the appropriate 3D printing technology for glasses and spectacles continues to be considered expensive. On top of that, you might also deal with other obstacles every time you use 3D printing technology.
As mentioned earlier, Nylon is the primary printing material used. But this material is still tricky to control because the frames’ finish is porous or rough, setting it apart from another material, acetate, known for its splendid finish. This makes acetate still the preferred choice. The 3D printing process is also slow. Traditional injection molding is high-speed, with the ability to produce 10/20 frames according to the mold’s capacity and the tool’s size.
How Cad Crowd can help
Cad Crowd is a trusted platform where you can find professionals who specialize in 3D printing glasses and eyewear services. With their help, you can transform your projects and take your business to a new level.