There are three major types of 3D models types: solid, wireframe, and surface. We base them on the methods and techniques used to create different 3D objects. CAD (computer-aided design) offers many other types, but most fall under those three.
Solid Model
Solid models deliver a 3D digital representation of an object with all the proper geometry. It is correct in all the other types, but “solid” refers to the model as a whole instead of only the surface. The object cannot be hollow. Much like all other types, solid models come from three-dimensional shapes.
You can use a myriad of basic and complex shapes. Those shapes function like building blocks that work together to create a single object. You can add more material to the blocks or subtract from them. Some CAD programs use modifiers, starting with one big chunk of solid, methodically carved out as if you were physically milling the base material in a workshop.
How Does It Work?
The basic technique is pretty straightforward in theory, but most agree that a solid model requires considerable computing power and is exceedingly difficult to master. The CAD software must simulate the object inside-out so that users can provide a proper cutaway. Doing this is necessary to reveal the mechanical properties of particular objects like an engine or its components. Solid models must allow for visualization and animation of the inner workings or moving parts of an object. Otherwise, they are concealed under the surface and hidden from plain sight during real-world application.
CAD programs use different procedures to build a solid model. Some add solid objects over another combination and placement to produce complex figures. Others extrude shapes from two-dimensional sketches to construct 3D assets. The result should be the same.
Regardless of the procedure, solid models almost always come from primitive shapes such as cubes, cylinders, prisms, spheres, and cones. The process can also start with multiple three-dimensional figures, allowing you to create pretty much every imaginable object. That includes not only machines and mechanical elements but also fantastical items and representations of natural things. Precise angles and dimensions are indispensable to building realistic visualization.
RELATED: 10 Free Sites for Free 3D Product Models and Great CAD Design Files
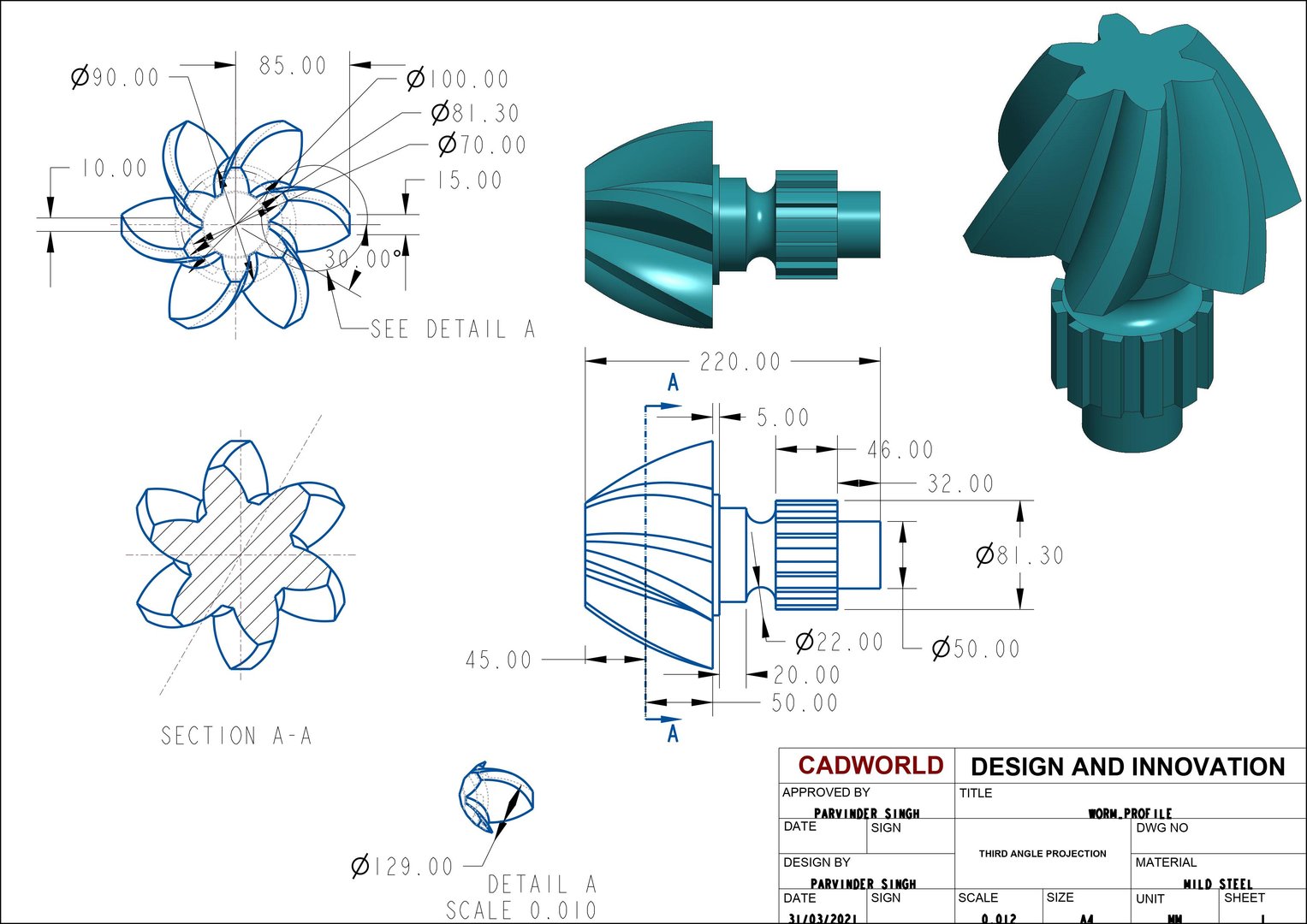
Many Other CAD Features
The actual complexity lies in the parametric features. Solid objects can be modified, subtracted, added, combined, transformed, and manipulated in all sorts of manners during the process without losing solidity. For example, you can subtract a portion from a cube to make a hole in the corner or center without changing the original structure. Some of the most popular CAD software for solid modeling include AutoCAD and SolidWorks.
Although the artistic touch of the modeler takes the leading role, CAD software does all the heavy lifting. It auto-calculates complex mathematical and engineering equations that would be time-consuming to do manually. However, the software relies on the information of mechanical geometry provided by the modelers. Extreme accuracy is of the utmost importance. Nearly every aspect of the design derives from mathematical equations for the software to solve. Therefore, incorrect geometry will lead to nothing but a mess.
For example, an automaker may want to build a brand new machine to challenge the record time in the Nürburgring by production cars. Perfect aerodynamic design for the type of engine and drivetrain is a top priority. You must translate car specifications with great precision per the design software. If need be, engineers will input data for every corner in the race track in relation to traction and wheel design. With any degree of inaccuracy, the software’s final product will not likely meet engineers’ expectations.
Euclidean Space
Every design component with finite size and clearly defined boundaries can be represented as a tangible object or part of an object. The area within the boundaries is Euclidean Space, an environment in which mathematically defined 3D drawings can be added, removed, and modified. Think of the space as a theoretical backdrop where each point of the model has its own coordinates. The points connect to build a 3D image. There are four key elements of a solid model, all of which should exist in the Euclidean Space:
- Complete: various points within the modelling environment classified as inside or outside. The purpose is to provide accurate division between the object’s surface and all else beneath it.
- Valid: edges, faces, and vertices must be connected in proper configuration to deliver a clear view of the 3D object.
- Unambiguous: design clarity and certainty. There can only be one single interpretation of all the design aspects drawn. A solid model must be realistic in the sense that the digital object represents its true shape in reality.
- Solid: the object needs to have true-to-life topological and geometric data including shape, size, weight, and connectivity of edges.
Historically, solid models were a verification and planning tool for assembly and machining applications. Now, we use them in many other industries such as product design, architecture, movies, and video games. In addition to AutoCAD and SolidWorks, other software for solid modeling is Tinkercad and FreeCAD for beginners. There is also a program called, Fusion360, which is better for more advanced users.
Advantages
- The final object is always mathematically correct, meaning the 3D model is always possible to fabricate in the real world.
- There are no myriad of triangles for drawing in extensive detail. Computational requirements can be lower, but it will increase with more complex objects.
- Extensive training is not always necessary thanks to the user-friendly tools. Anybody with an engineering background should be able to understand how objects are generated in the software.
Disadvantage
- The only massive drawback is that a solid model, no matter how advanced the software is, does not always represent organic shapes (because of their physical imperfections and irregularities) in a naturally realistic fashion.
Sophisticated modern CAD systems, however, can generate solid models of well-defined objects in full colors, displaying their entire surface with shadows and lights to accomplish lifelike quality.
Such systems are likely to require complete information about the object drawn to do the job correctly. Apart from the geometrical and topological data, the system needs better computing power to eliminate or minimize the possibility of human intervention in the design. Automation takes over not only the drawing process but also finite element analysis (a computerized method to determine how an object reacts to external forces such as heat, cold, vibration, water exposure, and other physical effects) and fabrication tasks generating commands for the CNC machining process.
Wireframe Modeling
In cases where the object features a lot of complex curves, wireframe modeling is often the method of choice. Basic building blocks of solid models basic shapes are sometimes too difficult to modify into the desired configuration and dimension. Wireframe modeling allows for a smoother transition between curved edges in intricate objects. As the complexity increases, however, some drawbacks become more apparent.
All surfaces along with the opposite sides and internal components normally hidden from view appear as visible lines with wireframe modeling. Although this method handles complex models in a way that solid models cannot, some say it is the quickest way for representing 3D images.
How Does It Work?
The basic representation of natural things may contain everything more than simple curves and flat surfaces. Many objects are nearly impossible to draw in 3D with realistic quality, even using sophisticated computers, by manipulating basic shapes like cubes and spheres. Organic shapes of people, animals, plants, and other objects have much more complex properties. When a solid model presents too many challenges in achieving realism, wireframe models come in handy. In this sense, a wireframe is more advanced than a solid.
The use of wireframe modeling in CAD comes from two major aspects: computer representation of an object, which concerns the structure of the model, and the computational procedures to manipulate visualization of the representation. Wireframe structures contain only two types of information—first, the geometric data in relation to the coordinate positions of connecting points in the 3D model. Second, the topological data that translate connected points as edges.
Wireframe Geometry
In other words, a 3D wireframe model goes together like a network of vertices. Three vertices (or triangles) make the basic element of wireframe models. The geometric face is composed of at least three vertices. You can adjust the shape and dimension of the object by making changes to each vertex position. One or more faces may share the same vertex.
More triangles create more realistic models. The “polygon count” indicates the total number of triangles contained within a wireframe model. In the old days, it was pretty typical to draw 3D objects or figures using low polygon count, resulting in a rather blocky object on the screen. Now that computer technology has developed a long way, it is not uncommon for wireframe models to use thousands, if not millions of polygons to achieve higher levels of detail. There is no limit to the number of polygons used. Using software run locally, a higher polygon count might not be a problem as long as you have decent hardware resources, but it might cause severe lag in web-based applications.
Advantages
- The ability to create more complex curves and surfaces than solid models
- In the final model, the only visible lines are the intersection of surfaces, not every single vertex
- The model contains enough information to transform it into solid model
Disadvantages
- The volume of the object is not defined
- You cannot remove lines otherwise hidden from view in the real world
- It’s difficult to interpret due to the myriad of intersecting lines
Like in solid modeling, it is possible to visualize the underlying design structure or highlight the object’s internal components (invisible in the real world). Common CAD software used for wireframe modeling includes Maya and Blender.
RELATED: Top 100 Sites for Free 3D Models and CAD Block Libraries
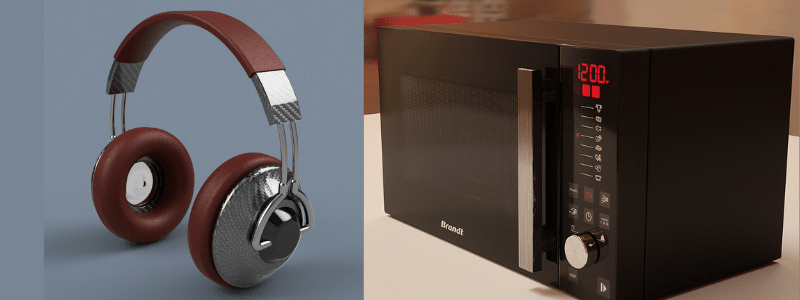
Surface Modeling
A higher step in terms of detail is the surface model. When seamless integration among the edges and a smooth transition from one vertex to the next is required, you need higher computational power to run the right software for building a surface model. Compared to the previous two, surface modeling is more demanding, but only because it has all the capabilities to create just about every shape that would be too difficult to attain with the solid or wireframe methods.
The primary purpose of a surface model is to showcase an object in 3D the way it is supposed to be visible in the real world. Cutaway is not needed, and networks of vertices are non-existent. Surface modeling is the most advanced of the three types of 3D modeling techniques. That said, it is easier to achieve than solid, although more complex than wireframe.
How Does It Work?
Surface modeling relies on an object’s positioning and curvature. It also matters how you can validate imperfections and apply smoothness across the image. The CAD software once again tackles the difficult task of calculating seamless connections between the guiding lines. For example, if you want to build a perfect sphere, the CAD software first needs an input indicating the frame structure of the surface, then the program covers or replaces the frames with smooth surfaces. In a sense, the process imitates the construction of a car body in which engineers build the supporting structure, then wrap it with a conforming metal enclosure.
Guiding lines are not the only option for achieving a good surface model. Some CAD software takes advantage of tangent planes or control points to determine the shape of the surface. A significant problem with this method is that visual representation of surfaces may contain geometry that cannot exist in the real-world, also known as non-manifold geometry (for example, a wall without thickness). Since they don’t exist, you cannot make them into physical objects. If the model is an object for fabricating, it is crucial to confirm if it is feasible to manufacture.
Object Exterior
Surface modeling, as the name suggests, focuses heavily on the visual representation of an object’s exterior. The object can be anything from organic shapes like fruits or animals, electronic devices like radio or phone, to complex structures like bridges and skyscrapers. Regardless of the object, surface models require clearly defined curves, contours, and textures of the outer shell. That said, an object can still be geometrically incorrect – without definite volume or thickness – in a surface model as long as you don’t plan to manufacture the model. The 3D image can still look good on screen because the laws of physics don’t apply to digital objects.
This flexibility gives designers the unlimited possibility to shape a model in a way that the solid modeling method cannot. On the other hand, you cannot slice open a surface model since the interior is empty; it is a hollow object. Depending on the application, you can represent the surface using polygons.
Advantages
- Complex surfaces are easily attainable
- They’re convenient where aesthetics are the main objective
Disadvantages
- Extensive training is necessary
- It requires more advanced programs and higher computational power
A complete aesthetically pleasing 3D model is possible with only surface modeling. However, when you physically fabricate the object, a combination of surface and solid modeling is often necessary.
How Cad Crowd can help
Cad Crowd delivers pre-vetted, high-quality 3D modeling and CAD services on-demand. Our network of qualified freelance designers and engineers are specialists in their fields.
We also provide a unique crowdsourcing option. Host a contest, post your design, and have our community submit their visual idea. Choose the best form out of the submissions, and pay when you find a winning strategy. Learn how you can launch a design contest within 15 minutes.
If you’re looking for assistance with a CAD draft or 3D model, find out how it works or contact us for a free quote.