The ultimate objective regarding spare parts management is to strike the perfect balance between the production cost of spare parts, the volume of parts that should be kept in stock, and lead time. 3D printing is one of the latest technologies that help suppliers and manufacturers alike achieve this goal.
As technology for digital manufacturing, 3D printing allows the storage of several spare parts in a virtual inventory and manufactured at the point of need, improving service and lowering storage costs. Due to the lower fixed costs, unlike traditional technologies, 3D printing is a more cost-effective option for low-volume production.
Therefore, it’s no longer surprising that many companies believe that utilizing 3D printing design services for spare parts paves the way for a more efficient after-sales market. Others also state that this technology can lower inventories and logistics efforts.
This article unlocks the advantages of 3D printing spare parts for your company’s success.
The dynamic world of spare parts
Spare parts manufacturers are currently dealing with numerous challenges that stem mainly from the storage and production of spare parts. One of these challenges is none other than the cost of ordering the spare parts themselves. Most things in traditional manufacturing are produced in volume to lower the overall cost for each piece.
Traditional volume manufacturing spreads costs across many parts. However, this model isn’t cost-effective for spare parts, which usually have lower production volumes. Additionally, locating and delivering the correct spare part to a global client can take weeks, negatively affecting customer satisfaction.
Moreover, manufacturers sometimes stop supplying certain spare parts, leaving customers without options. Companies also face challenges in determining the correct inventory quantity to store. Maintaining well-stocked warehouses is costly, especially with excess inventory.
In contrast, 3D print design experts can address these challenges effectively. This technology allows quicker production and delivery of spare parts in smaller volumes. On-demand printing eliminates the need for extensive inventories, reducing storage costs. 3D printing has significantly streamlined the spare parts production process.
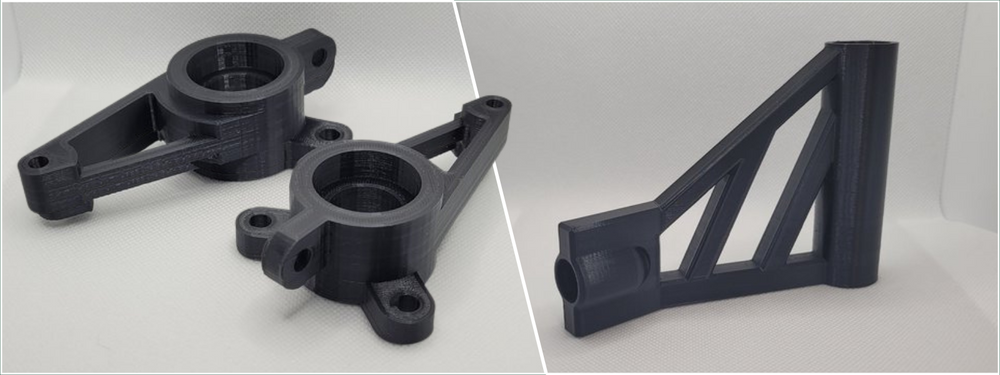
RELATED: An OEM’s guide to product design and manufacturing prototypes
Benefits of 3D printing spare parts
Take a look at how 3D printing solves issues in the industry of spare parts:
- Maintain a digital inventory
3D printing has reshaped how companies manage spare parts inventory, balancing investment with timely customer demand. The shift towards a digital inventory is facilitated by 3D printing’s ability to produce parts directly from digital design files without the need for tooling.
A digital inventory allows for storing spare parts, especially lower-demand or obsolete components, freeing up physical warehouse space in a virtual catalog. When a part is needed, it can be found in the digital inventory, sent to the 3D printer, and produced within days or even hours.
This shift from a make-to-stock to a more sustainable make-to-order model for low-volume spare parts brings significant advantages. Suppliers and OEMs can reduce the quantity of parts stored in warehouses, lowering inventory costs. Producing parts as needed allows for a more efficient and cost-effective approach to spare parts management.
- Economic production in low volumes
3D printing also enjoys lower fixed production costs, unlike traditional manufacturing processes such as vacuum forming and injection molding. Being a highly automated process, 3D printing doesn’t need pricey tooling.
In general, lower cost is also associated with the setup of the production equipment piece. These lower fixed costs are why 3D printing offers an economic benefit when producing parts in smaller volumes.
- Speedy lead times
Lead times of traditional manufacturing methods are usually measured in months because of the need to design and develop a tool and prepare a production line. On the other hand, 3D printing provides relatively shorter and, thus, faster lead times.
A tiny aluminum bracket, for instance, can be produced using DMLS technology in just a few days instead of the minimum of 12 weeks needed to manufacture it using metal bending and extrusion processes.
If a few obsolete parts are replaced without spare parts, 3D printing, and reverse engineering are undoubtedly ideal. 3D scanning service experts produce a 3D printable digital model of the spare part that will be sent to a 3D printer and developed faster. This process significantly allows manufacturers and suppliers to improve their business agility and flexibility.
Are there challenges to 3D printing spare parts?
While there has been an extensive recognition of the benefits that 3D printing spare parts can offer, bringing the technology as a part of the streamlined supply chain also has its challenges.
One of the main issues for most suppliers and OEMs is none other than process repeatability. Thus, the challenge here is to set the quality standards for spare parts and guarantee that the 3D-printed parts will match these standards and the industry specifications.
Using dedicated software plays a vital role in making sure that all standards are adhered to. Legal barriers also exist in the form of copyright and Intellectual Property that must be resolved.
With 3D printing design experts starting to shift manufacturing towards a more digitally-driven supply chain, uncertainties remain regarding IP and how copyright should protect the designs of parts that suppliers provide.
Before the spare parts industry widely adopts 3D printing technology, OEMs and suppliers must strengthen and ensure the security of their individual intellectual property.
RELATED: How 3D printing is changing product design and manufacturing
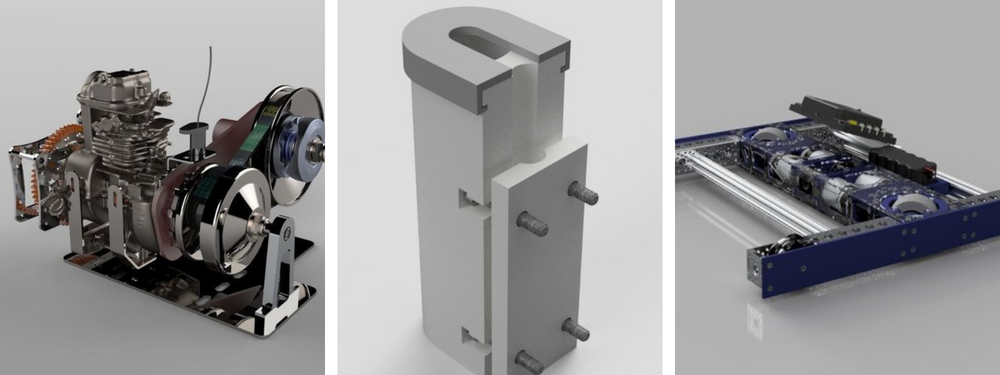
Which companies 3D print spare parts?
The following are some of the companies that are already starting to tap into the power of 3D printing spare parts:
- Jaguar
The technology of additive manufacturing is no doubt ideal for manufacturing car parts. It’s challenging to look for replacements, particularly for older vehicle models. However, the powerful combination of additive manufacturing, 3D modeling design services, and 3D scanning makes producing spare or rare vehicle parts possible.
Jaguar is a car manufacturer that has been taking advantage of 3D printing for manufacturing car parts for their old vehicles. They used 3D scanning to recreate their classic 1957 XKSS model. It took 18 months for the recreation to be completed.
While there were differences with the original car because of modern safety requirements and standards, additive manufacturing still allowed the recreation of the rare parts.
- Porsche
The Porsche Classic Division is a division dedicated to the classic vehicles of Porsche. 3D printing is used to produce spare parts for rare vehicles. Since these cars are rare, their original features are either no longer available or made these days. They are 3D printed instead to have accurate and fitting working components.
Additive manufacturing is a genuinely convenient and economical manufacturing process for small batches. That is precisely what happened to the rare Porsche 959’s clutch release level. The division used the SLM 3D printing technology for plastic, light metal, and steel components to produce certain 3D-printed parts.
- The Volkswagen Group
The Volkswagen Group understands additive manufacturing and all its benefits. They use 3D printing technology not only for spare parts but also for their tooling processes. The carmaker truly harnesses the potential of 3D printing to the next level.
- Whirlpool
Whirlpool originally started using 3D printing with spare parts. They are now digitizing their part catalog to prevent obsolescence. While the company manufactures many machines, they also require plenty of spare parts.
The production method is specifically used to produce spare parts for home appliances. Since most machines become obsolete at one point or another, it’s essential to have spare parts, and 3D printing allows Whirlpool to manufacture enough parts on demand at a lower cost.
How Cad Crowd can help
The future of 3D printing spare parts looks promising with advancements in technology. This innovation is expected to make its way into various fields and industries. If you are planning to print spare parts for your company or want to be prepared for future possibilities, Cad Crowd can assist you in finding experts who can help you achieve your goals and succeed in your niche. Our freelance 3D artists and CAD designers offer 3D printing services, and you can request a free quote to receive their assistance.